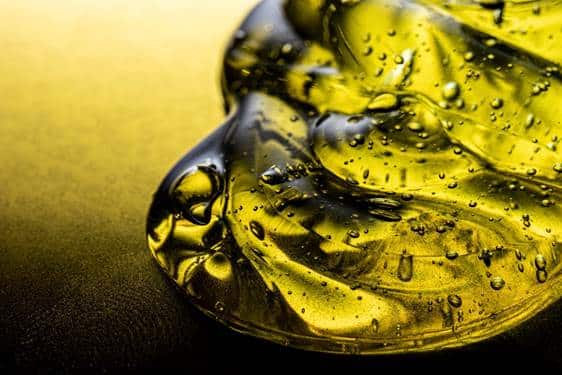
Tips for choosing the right lubricant for your industrial machinery
Choosing the right lubricant for your industrial machinery is crucial to ensure optimum performance and extend the life of your equipment. A lubricant not only reduces friction between moving parts, but also protects against corrosion and wear. However, selecting the right lubricant can be a challenge due to the variety of options available. Stay tuned to this article to learn about all the variables you need to consider for an informed and accurate choice.
Aspects to consider when choosing an industrial lubricant
When considering the use of an industrial lubricant, it should be kept in mind that choosing the right lubricant is essential for the proper functioning of machinery parts. The first decision in this regard is whether to use grease or oil, as these are the two fundamental groups of lubricants.
Below, we explain the factors that influence the choice of lubricant:
Machine where it is to be applied
When choosing the lubricant for your machinery, it is essential to consider the type of machine and its specific application. Each industrial machine has its own lubrication needs, which depend on factors such as type of motion, speed and load. For example, heavy machinery, operating under high loads and extreme conditions, requires a type of lubricant with high viscosity to withstand pressure and reduce friction. Whereas for machines with smaller, faster moving parts, a low-viscosity lubricating oil might be more suitable. In addition, operating conditions, such as extreme temperatures or extended downtime, also influence lubricant selection.
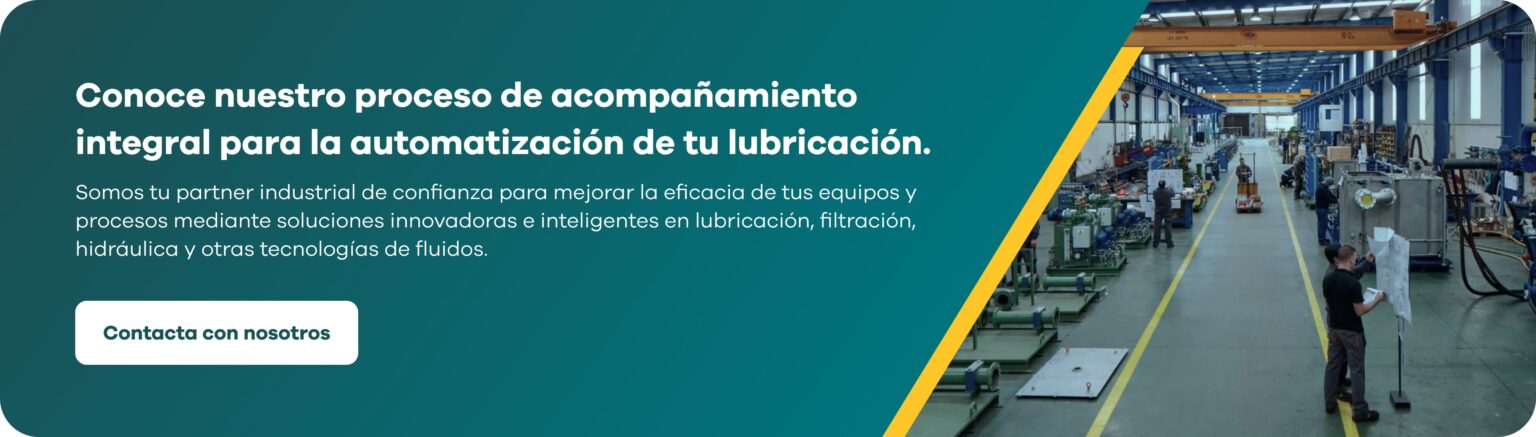
Lubricant-system compatibility
Compatibility between the lubricant and the system in which it is to be applied is another crucial aspect. Not all types of industrial lubricants are suitable for all systems; choosing an incompatible one can lead to lubrication problems such as material degradation or the formation of unwanted deposits. It is essential to ensure that the lubricant is compatible with the materials of machinery parts and seals. Additives present in lubricants, such as those that prevent corrosion or improve lubrication, must also be compatible with the system.
In addition, compatibility as a factor must also be taken into account when mixing different types of lubricants. In some situations, it may be necessary to mix lubricants, so it is crucial to ensure that the products are compatible to avoid adverse reactions. Incompatibility can cause problems such as accelerated oxidation of the base oil, leading to inadequate lubrication and system failure. Therefore, it is always advisable to consult the technical specifications of the machinery or lubricant manufacturer to ensure that compatibility is not an issue.
Base materials
The original raw material base of the lubricant is decisive for its performance in industrial applications. Lubricants can be composed of mineral oils, synthetic oils or a mixture of both. Mineral oils are derived from petroleum and are generally suitable for standard applications, while synthetics offer advantages in more demanding working conditions, such as extreme temperatures or high loads. Choosing the right base oil is essential to ensure the effectiveness of the lubricant under the specific operating conditions of each application.
The type of base stock also affects the lubricant’s service life and its ability to resist oxidation. Synthetic oils, for example, typically offer longer service life and better thermal stability, making them ideal for applications where maintenance intervals are long or operating conditions are severe. On the other hand, mineral oils can be more economical, but may require more frequent changes. Knowing the properties of base stocks helps select the right lubricant to maximize machinery efficiency and performance.
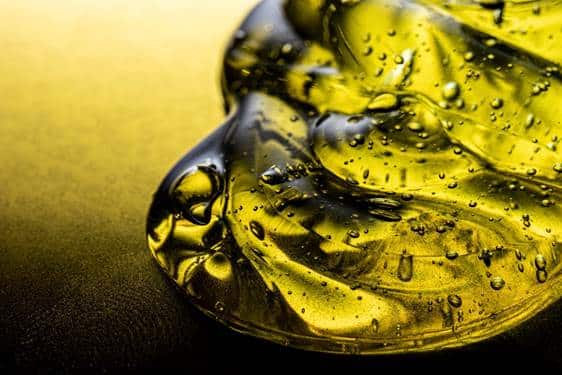
Lubricant composition
The composition of the lubricant, including the additives used, plays a crucial role in its performance. Additives can improve the properties of the lubricant, such as resistance to oxidation, protection against corrosion, or the ability to operate under high temperatures or extreme conditions. Choosing a lubricant with the right composition is vital to meet the specific needs of industrial machinery. For example, anti-wear additives are essential in applications where friction reduction is critical to protect moving parts.
In addition, the composition also determines the lubricant’s ability to provide adequate lubrication throughout the machinery operating cycle. In situations where exposure to contaminants is high, a lubricant with detergent additives can be beneficial in keeping the system clean and in good condition. Understanding the composition of the lubricant and how it interacts with the system helps ensure that the necessary protection and performance is provided under the specific conditions of each machine. This not only improves operational efficiency, but also extends the life of critical machinery components.
Por qué es Importante elegir el lubricante industrial correcto
Choosing the right industrial lubricant is critical to the efficient operation and longevity of machinery. The right lubricant not only ensures proper lubrication of moving parts, reducing friction and wear, but also protects against corrosion and rust. This is especially important in industrial applications where equipment is exposed to extreme conditions or prolonged downtime. A well-chosen lubricant can make the difference between smooth, efficient operation and costly failures or unplanned downtime.
In addition, using the right lubricant can mean significant savings in industrial machinery maintenance and repair costs over the long term. Proper lubrication helps prevent premature wear, minimizing the need to replace components and reducing machinery downtime. It also helps improve energy efficiency, as less friction means less energy needed to operate the equipment. In short, understanding how to choose the right industrial lubricant not only optimizes machinery performance, but also protects the investment and ensures a higher return on the investment made in industrial equipment.