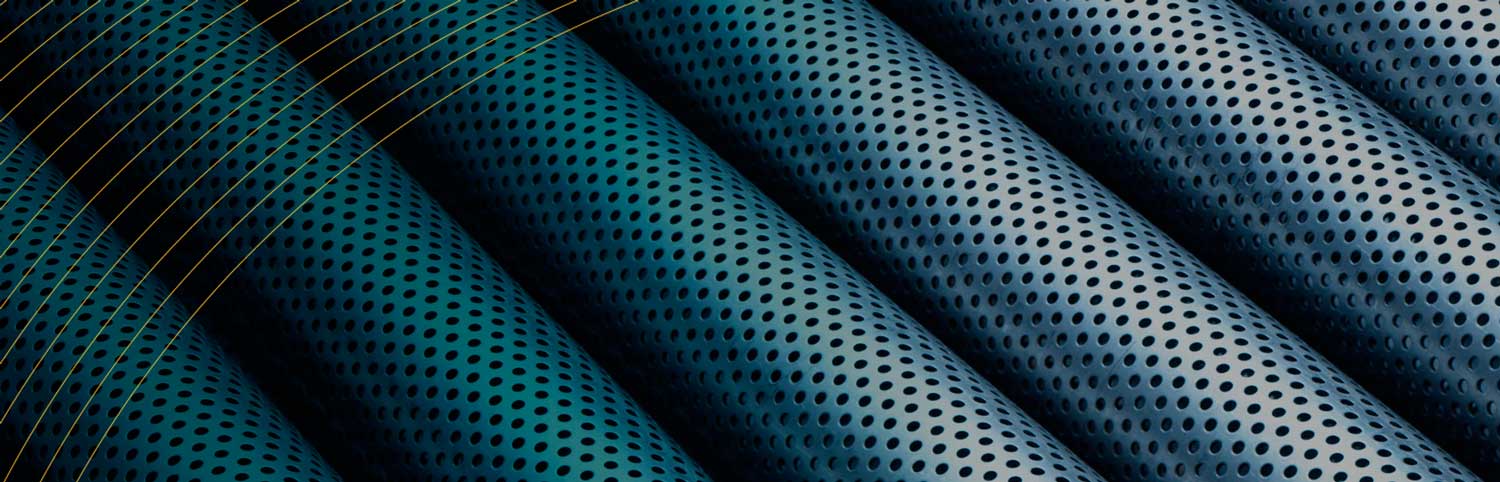
Services
360º traceability: find, in the same company, all the services you are interested in: from initial design and engineering, to manufacturing and after-sales service.
When all these phases during the development and assembly of a product go hand in hand under the umbrella of NORTEK, applying the highest demands in each of them, you can only obtain a 100% satisfactory solution for you, whether you are a manufacturer, engineering project manager or end customer.
Get to know our services and discover how you can improve your business thanks to each one of them.
Comprehensive lubrication and fluids technology solutions
100%
Engineers & manufacturers
The accumulated knowledge of more than 50 years at your fingertips
Engineering and consultancy
A firm of specialised engineers at your disposal
NORTEK is advice, research, design of customised solutions, carrying out preliminary studies and calculations for each project, as well as manufacturing and assembly. This is possible thanks to the team of expert engineers at our sites in Pinseque (Zaragoza, Spain) and Auburn (Massachusetts, USA).
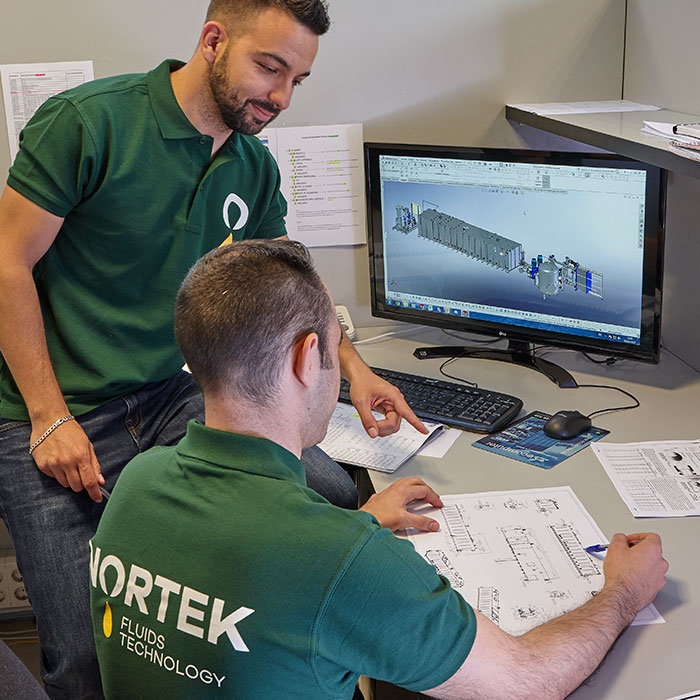
We like to think of ourselves as an engineering company that also has its own factory. The sum of all this results in 360° traceability as well as the development of lubrication and fluid management solutions, which we design from scratch specifically for you and which meet the most stringent regulatory requirements.
What do you get from our engineering and consultancy service?
These are some of our competences:
- Field data collection
- Tailor-made design of lubrication and cooling systems
- Calculation of oil consumption in bearings and rolling bearings
- Calculations of cooling requirements in gears
- Lubricant consultancy
- 3D simulations of fluid behaviour in reservoirs
- Calculation of filtration requirements
- Design of customised filters for any fluid
- Dimensioning, layout and optimisation of piping systems
- Flow meter calculations
- Design of approved pressure tanks
- Adaptation of equipment in existing plants
- Water, air or hydraulic fluid consumption calculations
- Supply of fluid installations for new plants
Engineering, a service in its own right
Engineering is one of the fundamental pillars at NORTEK, based on the knowledge accumulated over more than five decades and on our continuous R&D&I processes. An advantage that always works to your advantage.
Likewise, our long experience both in the renovation of old installations and in the integral supply of new plants makes us your reliable partner to review lubrication and fluids installations for technical audits, optimisation and renovation.
We manufacture our own products
In-house manufacturing, total control at all stages of the process
In-house manufacturing, together with the work of our engineering department, is one of the great hallmarks that define us, allowing us to be flexible and show an agile response capacity.
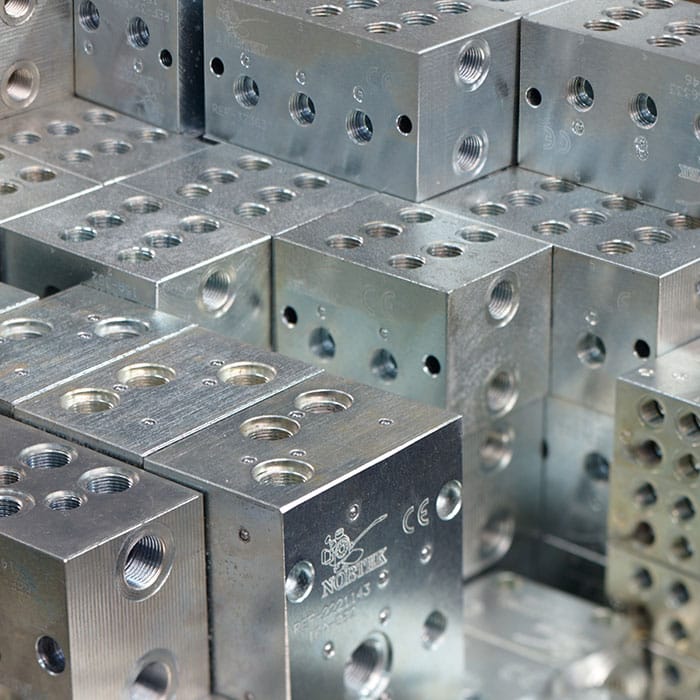
We are a multi-purpose production plant, in which we continue to focus on in-house manufacturing, in-depth knowledge of products and processes, and the most demanding quality control.
What are the advantages of in-house production?
You will have a team of specialists at your side who will be able to take care of everything:
- Machining of components for the control, conveyance and distribution of fluids
- Production and assembly of components for the distribution of grease, oil and air-oil.
- Small and large boiler works
- Filters and filter elements
- Welding certified according to ISO 3834-3
- Blasting and painting of components up to 24 m and 12 t
- On-board piping execution on customer’s equipment Manufacture of base plates
- Design and programming of electrical panels
- Handling of stainless steel components in separate hall
- Quality control
From engineering office to in-house manufacturing workshop
Our boiler, machining, precision and electrical workshops, together with our blast and paint shops, supply most of the components and operations necessary for the production of our systems.
This is why we have the capacity to materialise what we design with a high level of self-sufficiency thanks to the specialised personnel present at all stages of the production process.
Research and development
Research and development: ready for the next challenge
Our involvement in a wide range of industrial sectors and processes (from iron and steel to petrochemicals, mining, paper, power energy and many others) allows us to keep abreast of the specific needs of each application, especially in terms of fluids and heat transfer.
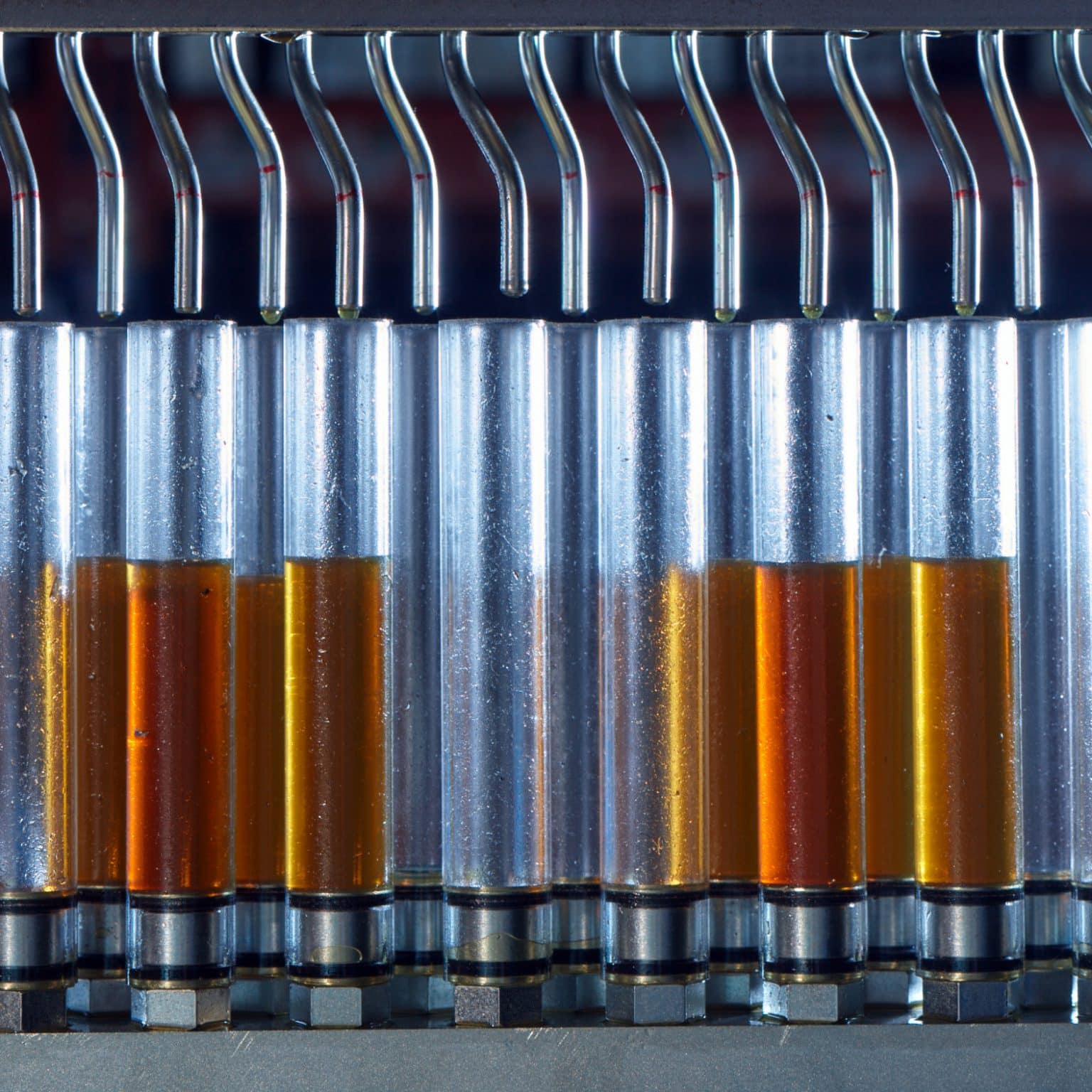
We like to ask ourselves about the new challenges facing the companies we work with, as well as the problems that have traditionally been difficult to solve. This puts innovative and efficient solutions within your reach when you need them.
Innovation is a key factor at NORTEK. Our engineers are ready to take on new challenges and proactively propose both innovative developments of existing technologies and radically new products. These projects also undergo extensive testing, first in laboratory conditions and then in the field.
How can our work in research and development help you?
There are many advantages to be gained from working in research and development, among which we highlight:
- Development of new filtration, fluid separation and heat transfer technologies
- Research into new cooling systems
- Research into fluid distribution systems (particularly lubrication)
- Development of new systems for optimisation of fluid-related industrial processes
- Innovation in internal manufacturing methods for products
- 3D printing
The fact that we have our own multi-purpose workshop and expert on-site service teams allows us to focus our developments not only on the product itself, but also on the feasibility and optimisation of its manufacture, assembly and operation.
Assembly, commissioning and maintenance
A product designed from start to finish for you, requires careful assembly for a correct start-up.
In addition to our own workshop staff, you have at your disposal a whole team of field fitters, including specialists in piping, hydraulics and welding. In this way you will have a proven quality assembly service, focused on achieving careful execution in minimum time, with special attention to the particularities and requirements of each project.
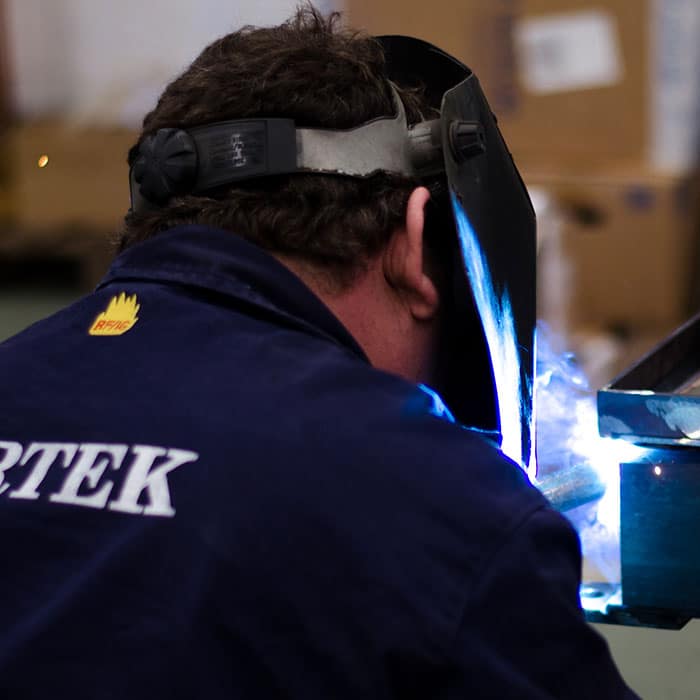
Some of our competences in this field are:
- Installation of lubrication equipment
- Field fabrication and installation of piping of any dimension
- Execution of water, air, hydraulic, oil, grease or air-oil lubrication installations
- Commissioning of equipment
- Specialised supervision of assemblies
- Equipment consulting (troubleshooting)
- Regular maintenance of lubrication equipment at the customer’s site
- Specific maintenance of installations during production stoppages
- Repair of pumps
- Repair and repainting of tanks
- Recovery for use of lubrication equipment, magnetic separators, vacuum dehydration systems…
Taking our fluid technology around the world
NORTEK’s engineers and field technicians also have many years of experience in supervising assemblies and carrying out on-site commissioning.
Our exporting vocation and the high level of complexity of some of the projects we have undertaken set us apart: we are prepared to travel around the world and to adapt to the cultural and technical conditions of any destination.
We also have personnel specialised in the maintenance of on-site lubrication systems, which we offer both on a regular basis and at specific times when the system is down and when it needs to be re-set up. This is complemented by the availability of our workshop to carry out in-depth repairs on equipment whose use is to be extended.
After-sales service
The delivery of your finished product is only the first step.
We firmly believe in long-term relationships based on trust, and we show this through our involvement before, during and after your order. Because we know how reassuring it is to be backed by a team of experts capable of advising you, and dealing with any incident, in a short period of time.
We accompany you on the road to optimal operation of our systems by means of precise documentation, proactive incident monitoring, trained technical support and rapid response in the supply of spare parts.
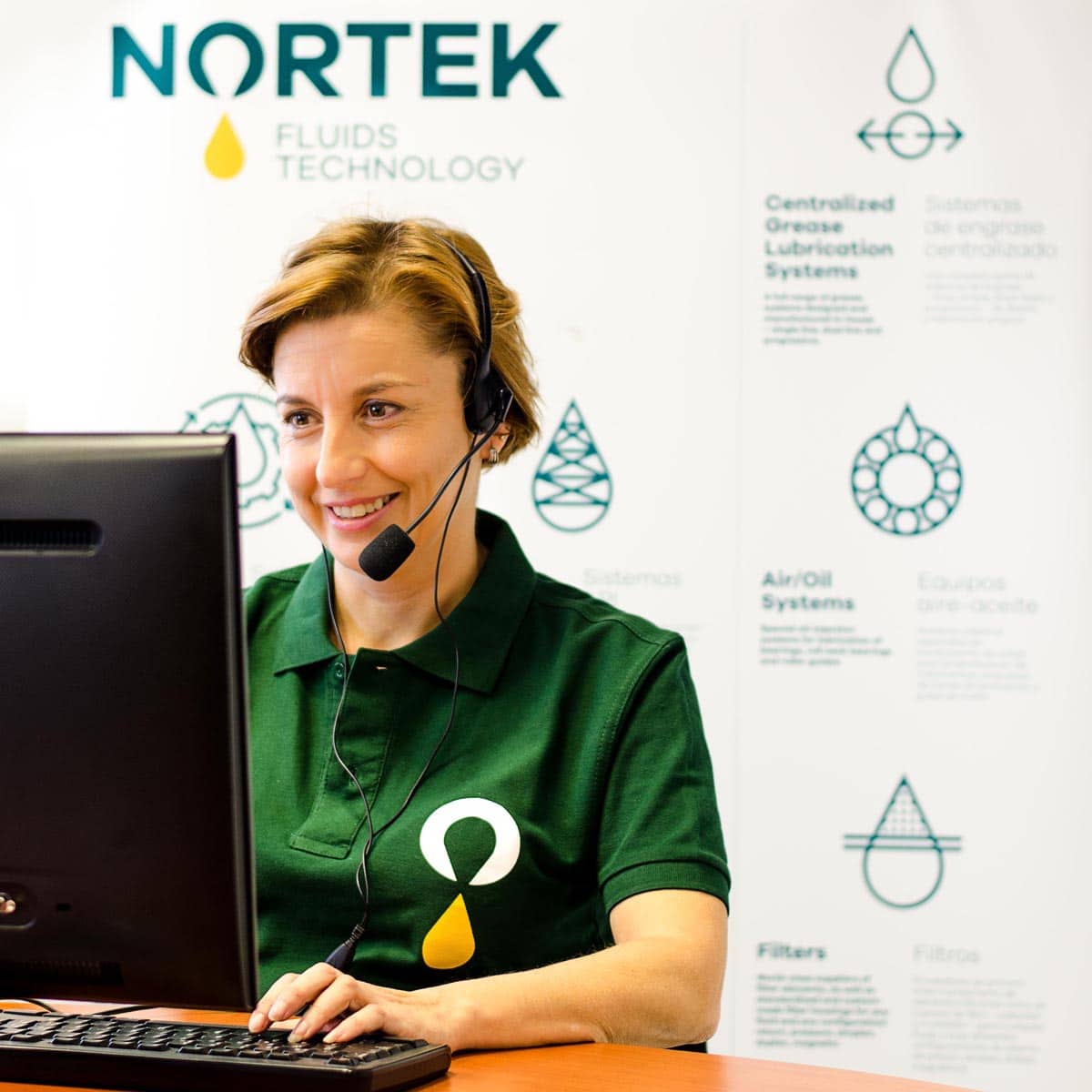
Engineers and manufacturers: you have everything in your favour
Our dual status as engineers and manufacturers enables us to offer you direct advice on the technical modifications necessary to adapt the configuration of our systems, in the event of variations on the initial operating conditions.
These are some of the services that distinguish our after-sales service policy:
- Monitoring of installed equipment
- After-sales technical advice
- Accompanying the customer in case of changes in operating parameters
- Supply of original and guaranteed NORTEK spare parts
Training and knowledge transfer
We share our knowledge of fluid technology with you.
We are aware of the importance of training technical staff to further improve their skills and therefore we offer specific training in our facilities or in your own company.
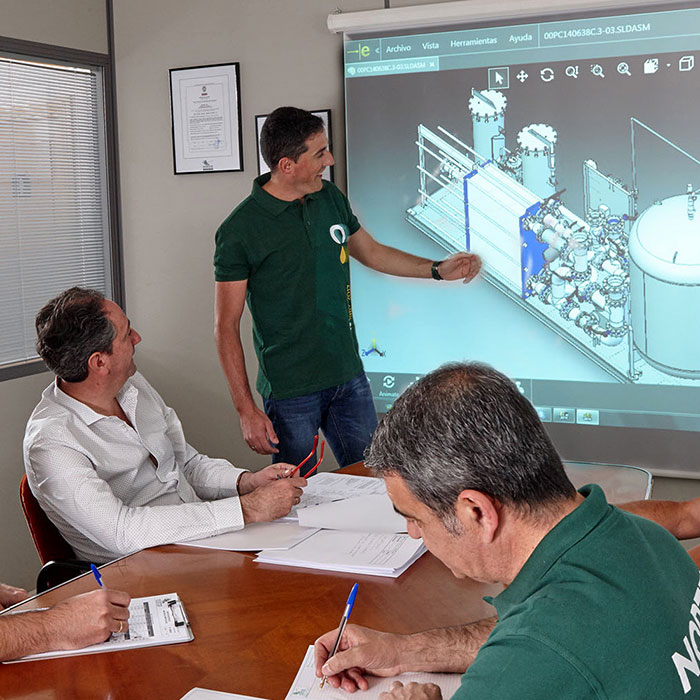
Specifically, we offer you:
- Tribology training sessions.
- Customer specific courses on lubrication, grease systems, vacuum oil dehydration, filtration systems and fluid systems (including cooling systems, hydraulics and pneumatics).
- Training sessions in our workshops on the commissioning of NORTEK equipment.
Throughout our long history, we have been called upon on many occasions to train technical personnel both in the theoretical bases of our fluid engineering and in the practical side of the operation of our systems. Our engineers and workshop technicians are at the customer’s disposal to facilitate this transfer of knowledge and promote a deeper understanding of the equipment we supply.
Customers who trust Nortek
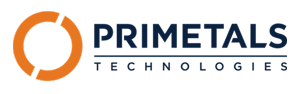
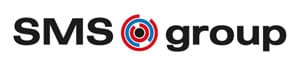
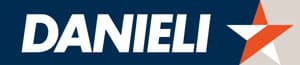
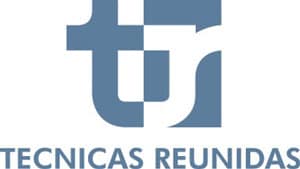
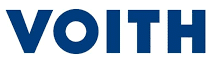

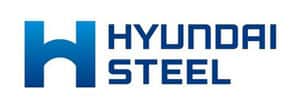

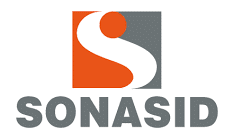
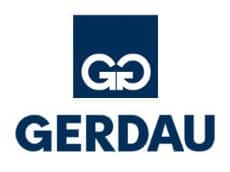
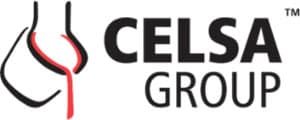
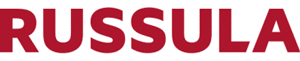
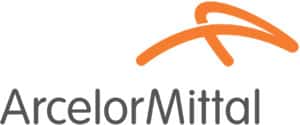
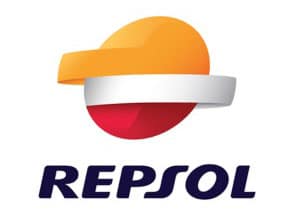
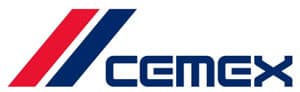
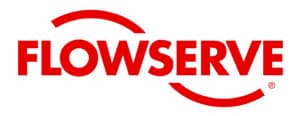
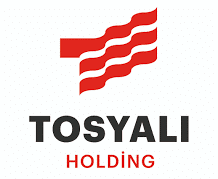
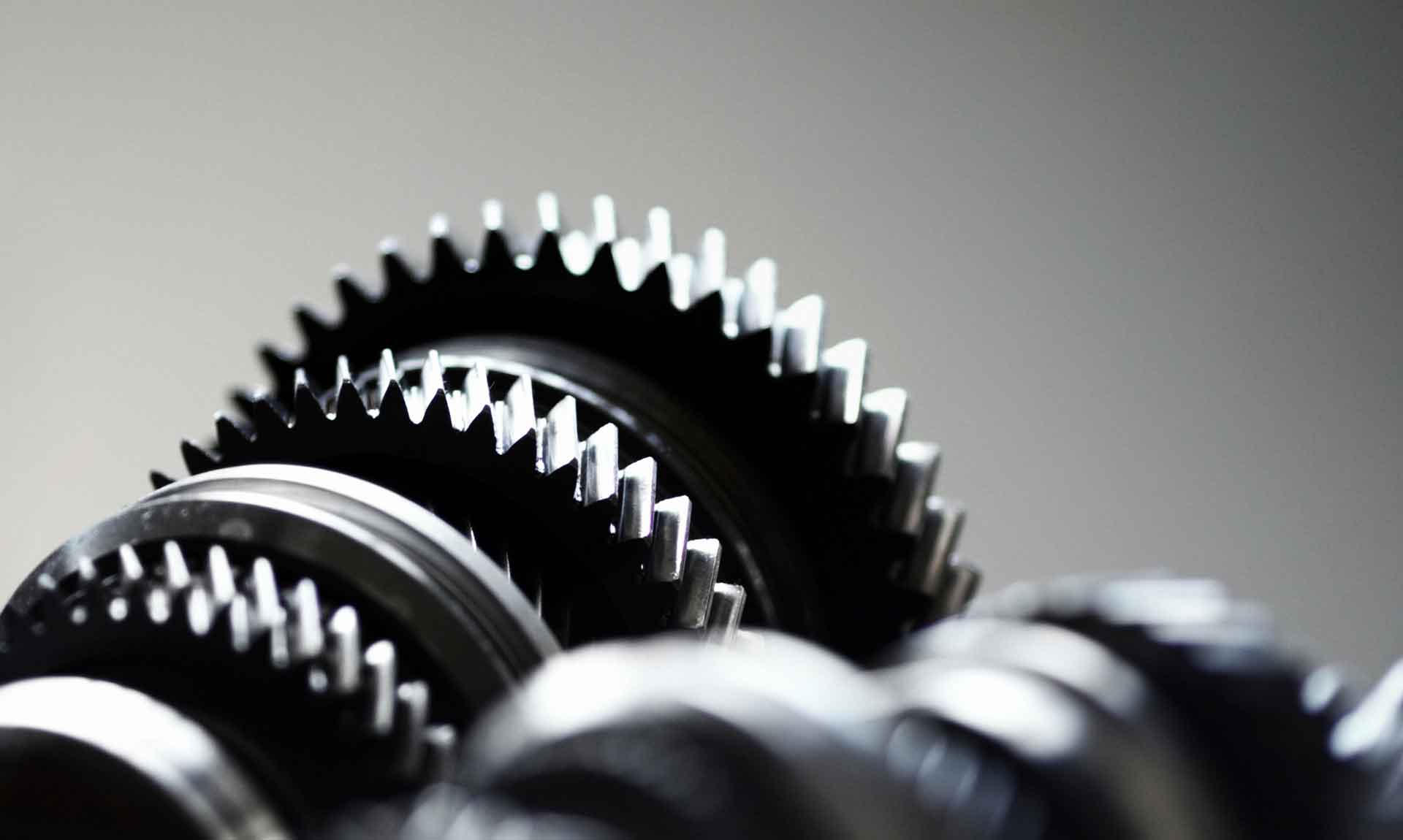
We work under the guidelines of the ISO 9001:2015 standard.
Quality and efficiency
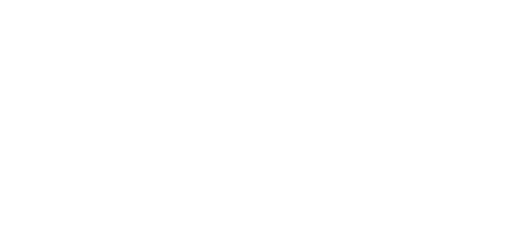
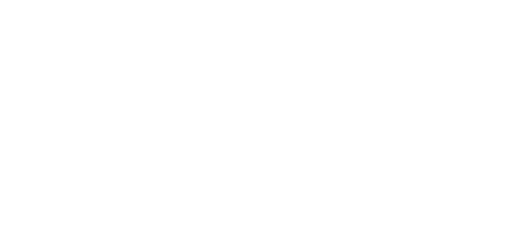
All members of NORTEK must know the quality policy, understand it and assume it as their own; and all of them are also called to contribute to the permanent task of evaluating, adapting and improving it.