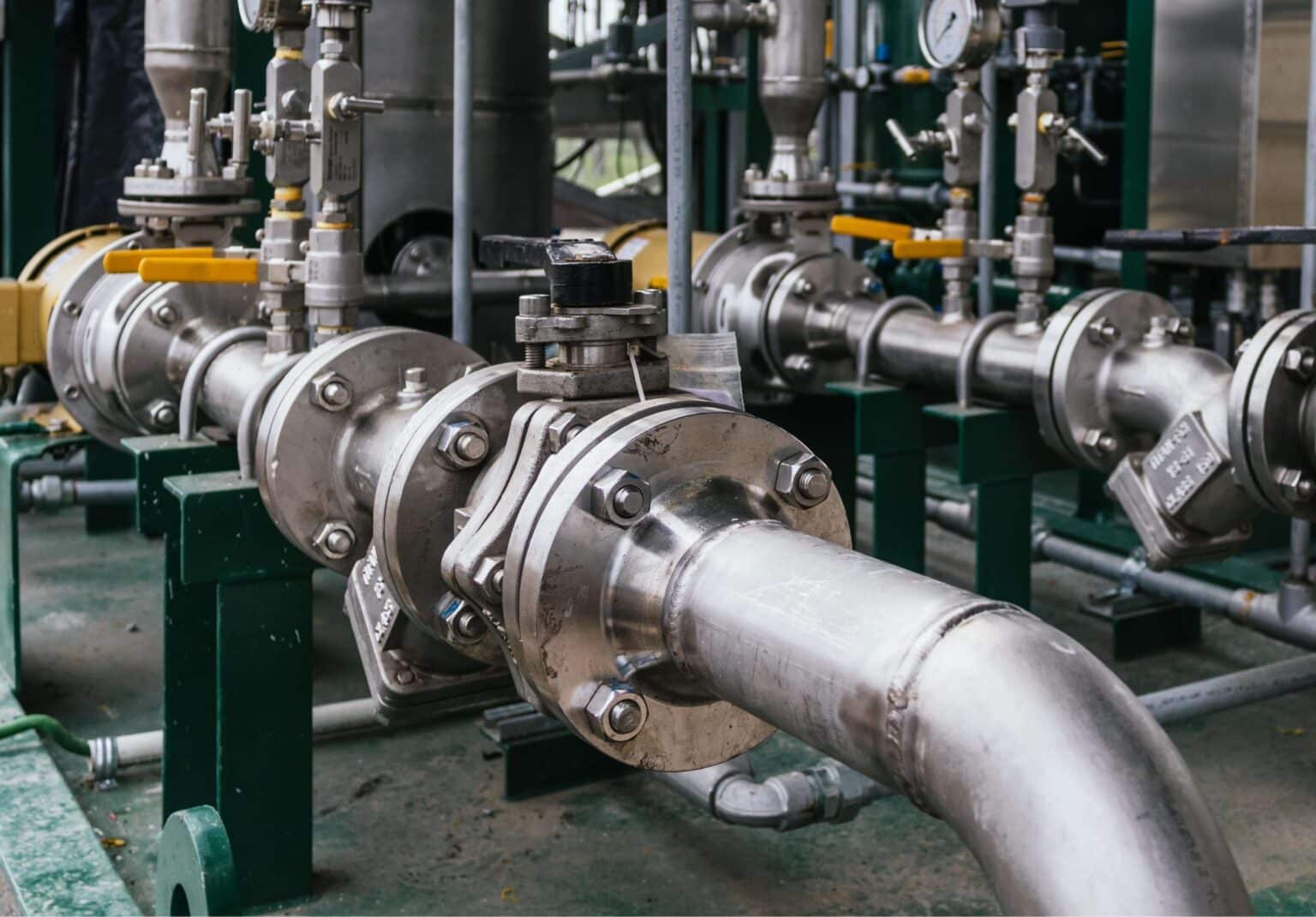
The most common lubrication problems and their consequences
Lubrication is a critical aspect in the efficient operation of any industrial machinery. Proper application of lubricants can significantly extend equipment life, reduce friction and minimize wear. However, common lubrication problems can arise from improper practices, leading to costly and damaging consequences. Understanding the most common lubrication problems and how to prevent them is critical to keeping machinery in optimal operating condition.
Why is lubrication of your machinery important?
Lubrication is essential for the smooth and efficient operation of industrial machinery. A well-maintained lubrication system reduces friction between moving parts, preventing premature wear and rust. This not only extends component life, but also improves operating efficiency and reduces maintenance costs. In addition, a proper lubrication program ensures that every part is properly greased, optimizing performance and reducing the risk of unplanned downtime.
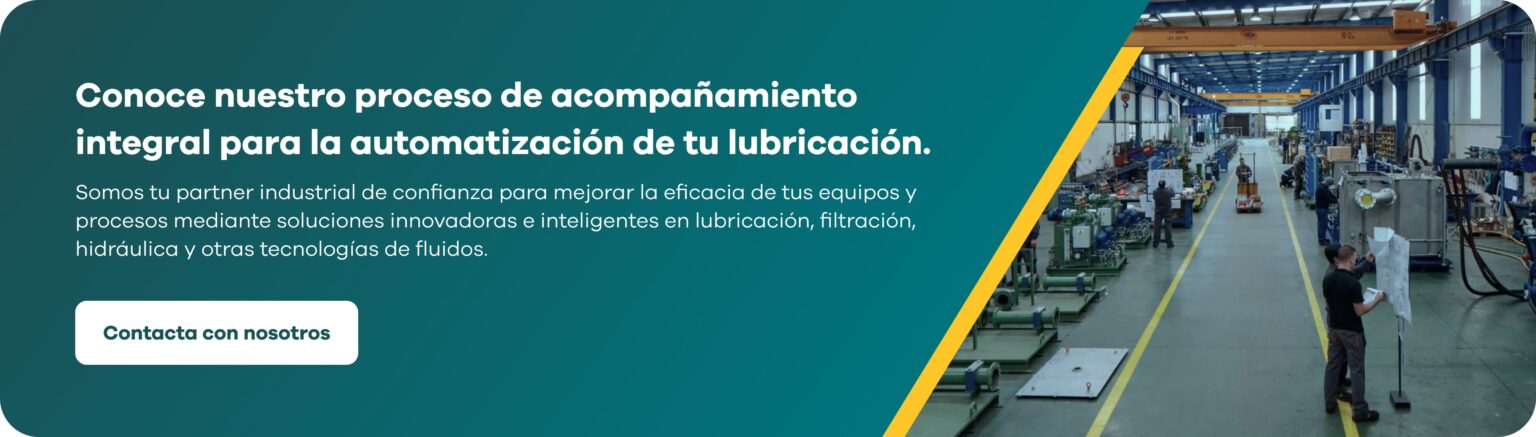
Main lubrication problems
We often find patterns in the various problems generated by the misuse of lubrication. The most frequent failures in day-to-day lubrication management (usually generated by manual or rudimentary lubrication) are the following:
Insufficient lubrication
Lack of lubrication is one of the most common problems in industry. When the lubrication system does not provide sufficient lubricant, the moving parts of machinery are exposed to excessive friction. This friction can cause accelerated wear of components, reducing their service life and increasing the risk of mechanical failure. Insufficient lubrication can also lead to an increase in operating temperature, which in turn can further damage equipment and increase the risk of rust.
Excess lubrication
Over-lubrication can be just as damaging as under-lubrication. Applying more lubricant than necessary can cause increased pressure inside seals and gaskets, which can lead to leaks and contamination of the working environment. In addition, excess lubricant can build up and trap contaminants, contributing to the formation of deposits and sludge that affect machinery performance. This not only increases maintenance costs, but can also cause irreparable damage to internal machine components.
Lubricant contamination
Lubricant contamination is another common problem in industrial lubrication. Contaminants such as dust, water and metal particles can enter the lubrication system, degrading the quality of the lubricant and reducing its effectiveness. This contamination can increase friction, causing premature wear and damage to mechanical components. In addition, contaminants can cause rust and corrosion, further compromising the integrity of machinery.
To prevent lubricant contamination, it is crucial to implement an efficient filtration system that removes contaminants before they can affect the lubricant. Regular inspections and maintenance of the lubrication system are essential to identify and correct any source of contamination. In addition, properly storing lubricants in controlled conditions can prevent the introduction of external contaminants. By following these practices, companies can improve the reliability of their lubrication systems and extend the life of their machinery.
Use of the wrong lubricant
Using the wrong lubricant is a mistake that can have serious consequences in industrial machinery. Each type of machinery requires a specific lubricant with appropriate viscosity and temperature resistance properties. Applying the wrong lubricant can cause increased friction, overheating and excessive wear of components. This not only affects operating efficiency, but can also lead to costly mechanical failures and unplanned downtime.
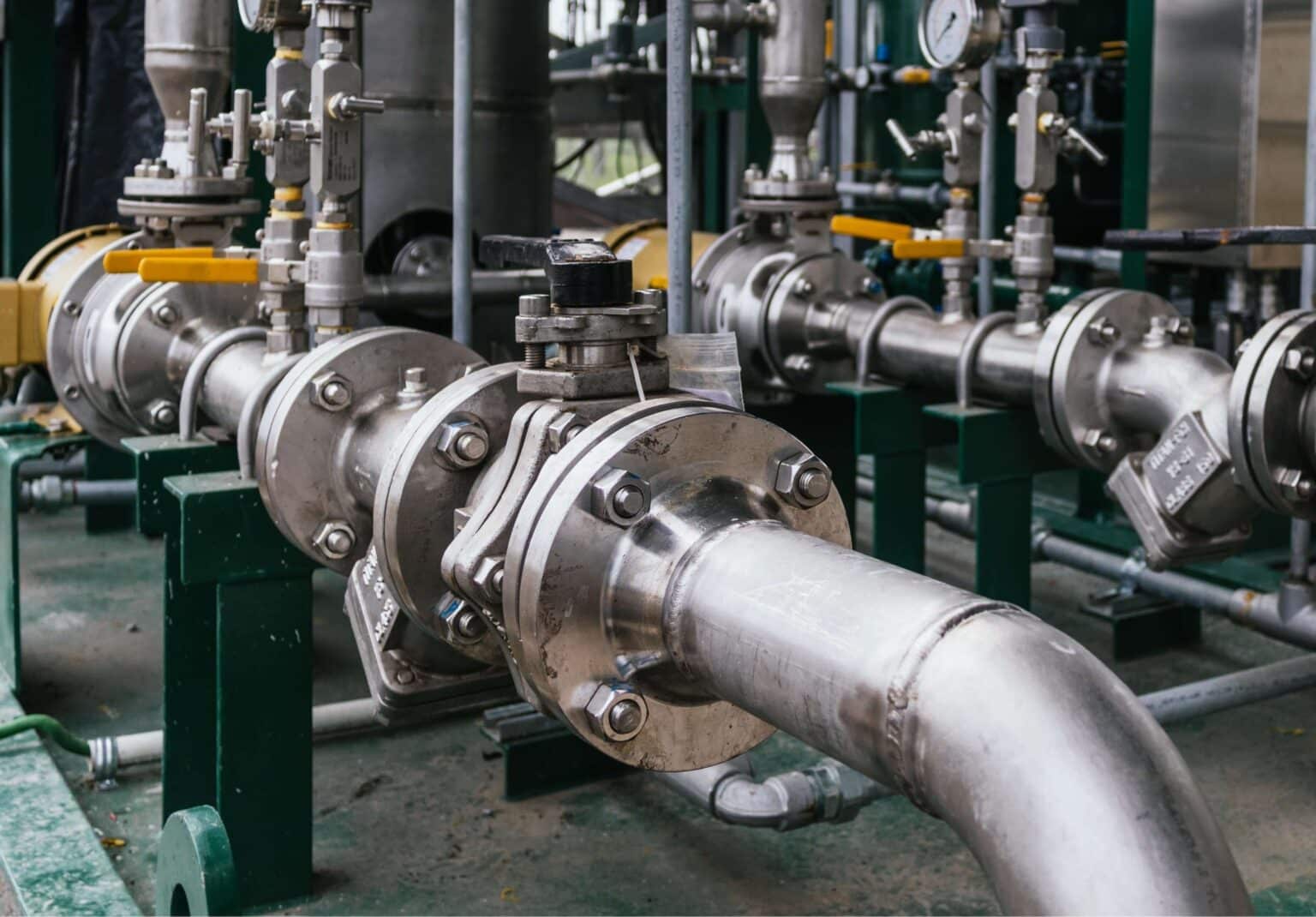
Consequences of poor lubrication
The consequences of poor lubrication can be devastating to any industrial operation. Excessive friction resulting from poor lubrication can cause accelerated component wear, reducing component life and increasing maintenance costs. In addition, poor lubrication can lead to increased operating temperatures, which can cause thermal damage to components and increase the risk of mechanical failure. These problems not only affect operating efficiency, but can also result in unplanned downtime and significant production losses.
Poor lubrication can also cause irreparable damage to critical machinery components, which can require costly replacements and long downtime. In addition, mechanical failures induced by inadequate lubrication can contribute to an unsafe working environment, increasing the risk of accidents and injuries.
How to avoid mistakes in industrial lubrication
To avoid mistakes in industrial lubrication, it is essential to implement a comprehensive lubrication program that considers the specific needs of each machine. This includes selecting the right lubricant, determining the correct quantities and applying it at appropriate intervals. A well-structured lubrication plan should be based on the manufacturer’s specifications and consider factors such as operating temperature, workload and environmental conditions. In addition, regular inspections and preventive maintenance are crucial to ensure the proper functioning of the lubrication system.
In addition to following a proper lubrication plan, it is important to train personnel in lubrication best practices and early identification of potential problems. The use of advanced technologies, such as lubricant condition monitoring and vibration analysis, can help detect problems before they become critical failures. By taking a proactive approach to industrial lubrication, companies can improve operational efficiency, reduce downtime and extend the life of their equipment, ensuring a profitable and sustainable operation.