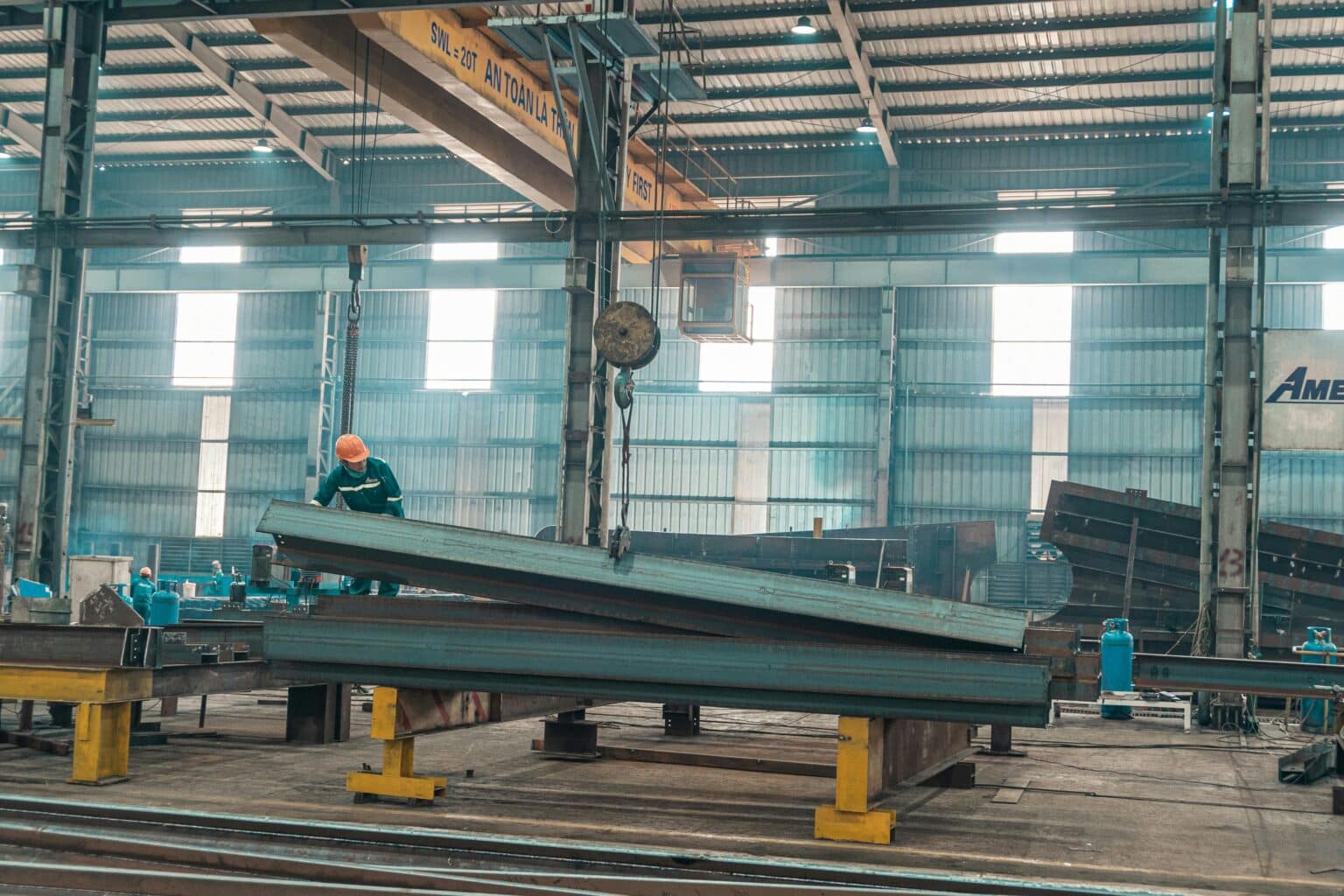
What is a technical shutdown and why is it necessary in the industry?
Technical shutdowns (also known as maintenance shutdowns) occur in industrial companies, usually during the summer or winter season. This is due to the fact that, during these dates, there are usually holiday periods, which leads companies to stop or substantially slow down production.
Read this article to find out what these stops are, why they are important and how to perform them as efficiently as possible.
What is a technical or maintenance shutdown?
A technical shutdown is a process carried out by factories and other industrial companies in order to carry out preventive work or necessary repairs. These shutdowns can also be dedicated to improvements in production capacity or in the facilities in general.
In order to carry out this process, the factory’s production process has to be totally or partially stopped, which requires both good planning and a sufficient level of resources so that the process does not take longer than necessary.
Why are technical shutdowns important for maintenance and safety?
Shutdowns, if carried out in an organized manner, can be a guarantee both for the long-term efficient continuity of the production process and for the safety of workers and the working environment. Below, we explain all the dimensions of this influence.
Improved efficiency and productivity
A well-planned technical shutdown allows for the overhaul, maintenance and upgrade of industrial equipment and systems. This process is critical to identify and correct problems before they become major failures, which in turn reduces unplanned downtime.
This process is carried out by proactively maintaining and upgrading equipment, thus achieving direct or indirect increases in efficiency and productivity.
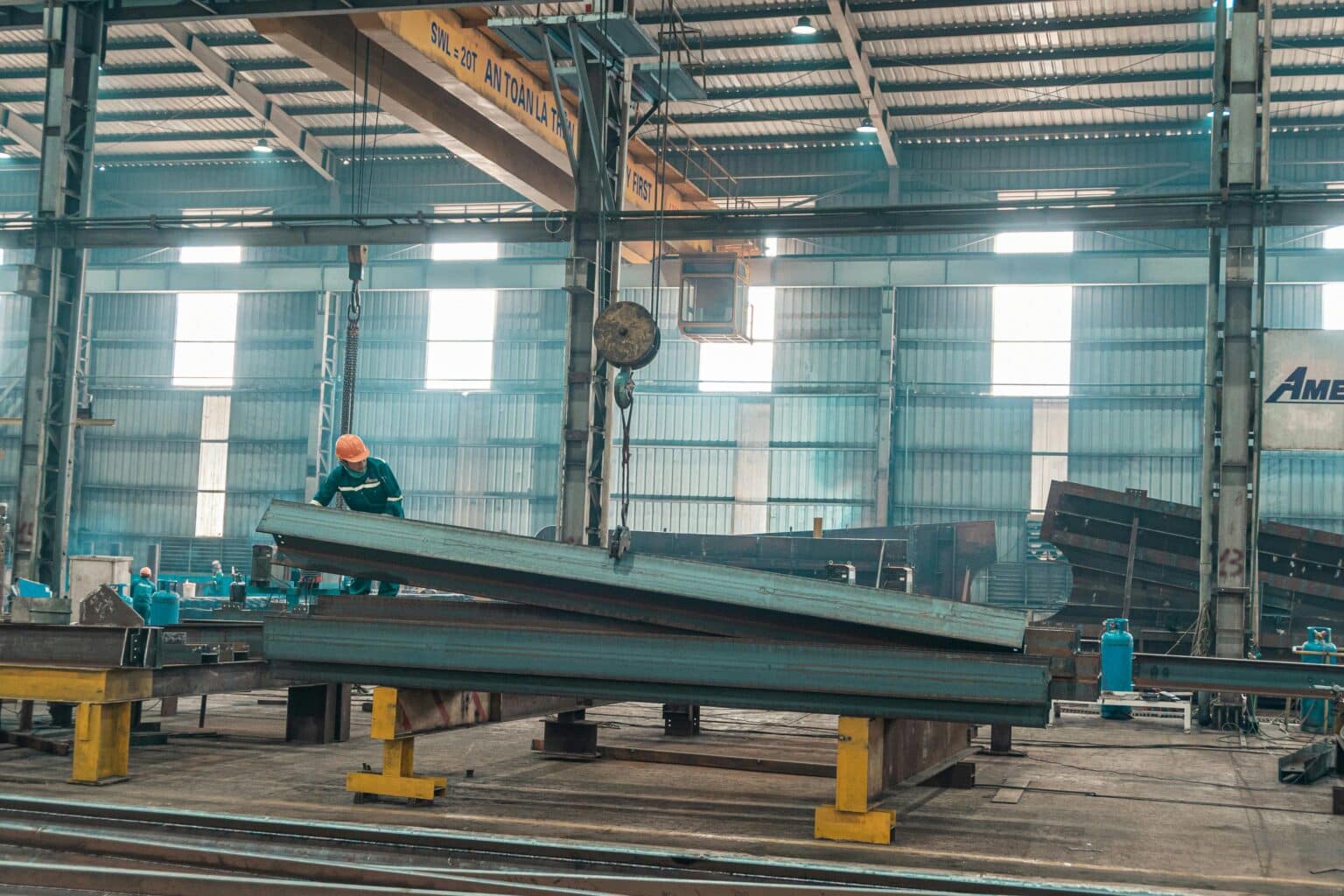
Increased security
Safety has to be the first priority in any industrial environment. Technical shutdowns play a crucial role in identifying and mitigating potential risks that could endanger workers and infrastructure.
Technical shutdowns can be used to carry out safety inspections to detect and correct possible errors in the installations and to train personnel in new standards and processes.
Reduction of Operating Costs
Although technical shutdowns require an initial investment in time and resources, in the long term, they are an effective strategy for reducing overall operating costs.
This is because they can avoid future costly repairs and improve the company’s use of resources, thus reducing the costs involved.
Regulatory Compliance
Industries are subject to various regulations and standards governing safety, the environment and operational efficiency. Technical shutdowns are key moments to ensure that these regulations are complied with or to update the processes they regulate.
Audits, certifications and protocol updates can be performed during shutdowns.
How to optimize technical stops?
The key point that optimizes maintenance shutdowns to the maximum lies in advance planning. This is based on predictive maintenance, which is responsible for predicting possible failures before they occur. Therefore, it is essential to have this type of maintenance fully monitored and enforced.
In order to optimize technical shutdowns, it is necessary to work on a preliminary organization phase that perfectly defines all the aspects related to the shutdown, such as its duration, the resources needed to execute it and the setbacks that may arise.
However, the rest of the maintenance processes also have an influence on technical shutdowns. Having a maintenance plan that is strongly committed to preventing and detecting errors in advance and correcting them when there is no other option, will help to reduce maintenance downtime as much as possible and make it as efficient as possible.