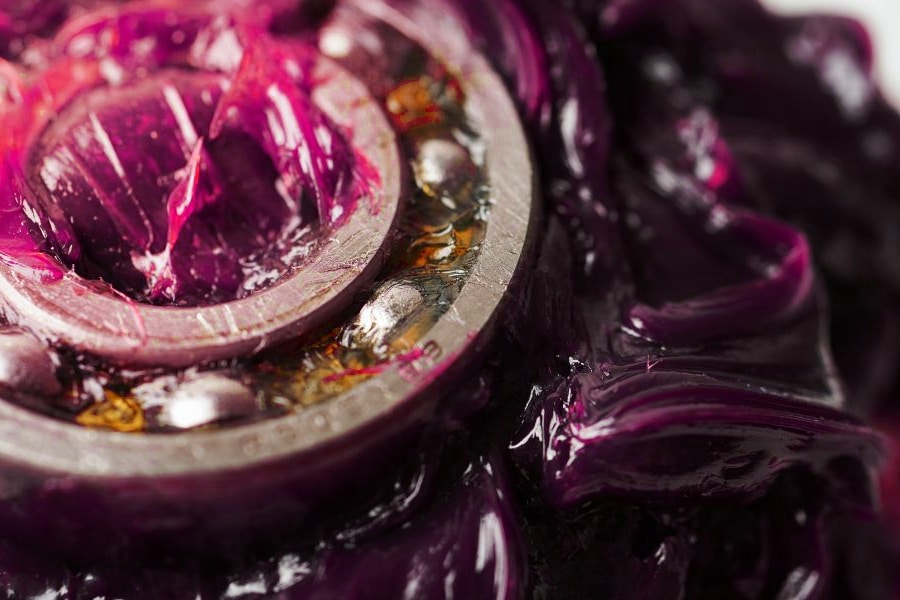
Uses and applications of lubricants for different metals
The uses of lubricants in the metal parts of each machine are diverse and cover a wide range of functions. Their presence is key in the operation of these and can make the difference in achieving maximum performance.
In this article we will explain their importance, their variants and their different uses.
The importance of lubricants
Industrial lubricants are crucial for machinery systems to function properly, as they help to ensure that the contact between bearings and other metal parts does not experience unexpected temperature increases due to friction.
They also prevent wear of the parts they protect, which reduces downtime and greatly increases the service life of the machine.
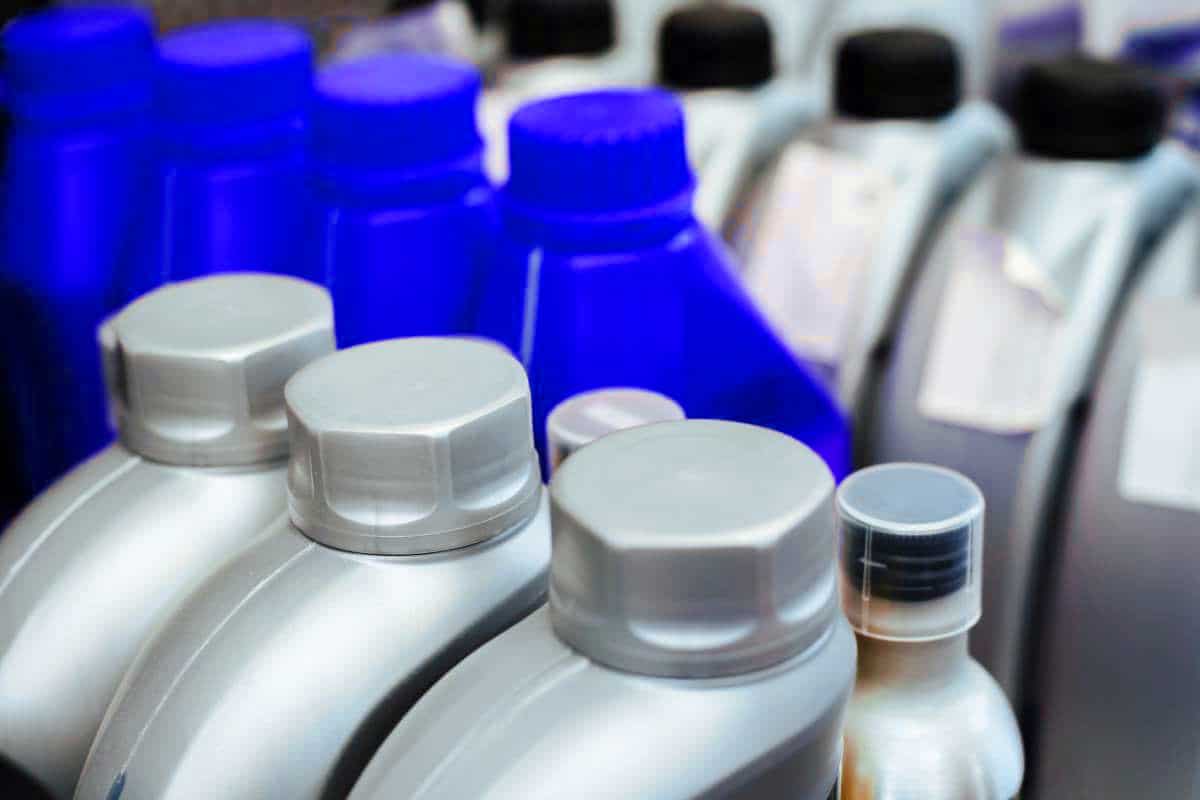
Types of lubricants
There are three types of lubricants according to their degree of solidification at room temperature: oils, greases and pastes. By the nature of our systems, we work mainly with the first two, but pastes also have a certain presence in the lubrication world.
Oil
Oil is a liquid lubricant with different viscosities, which allows it to be moved and distributed more fluidly. It is usually made with a base made from petroleum derivatives to which various additives are added.
Their composition and characteristics can vary greatly depending on their specific application, but they are normally used in high-speed machinery.
Grease
Greases are composed of a base oil to which a thickening agent is added. This gives them different characteristics from oils, providing them with a unique consistency and adherence, allowing them to last longer on contact surfaces.
Paste
Pastes are unctuous substances that contain a high percentage of solid lubricating particles, so they can also be considered dry lubricants.
This characteristic allows the pastes to have a high structural stability, facilitating a precise application on the area to be protected (as they do not drip or spill).
The different uses of lubricants
The lubricants mentioned in the previous section cover a wide range of functions. Although the main one is to lubricate the key points of the machines, they play very important roles in other aspects, all in order to maximize the performance of the manufacturing processes.
Lubrication
One of the main functions of lubricants is to reduce friction between the tools and moving parts of machinery, which prevents premature wear and extends their lifespan.
In any operation where there is contact between two metal parts, friction reduction is key to prevent deformation, wear and tear that can damage the final product.
The main function of lubricants is to prevent this friction. It is the feature that has the greatest impact of all on machine performance.
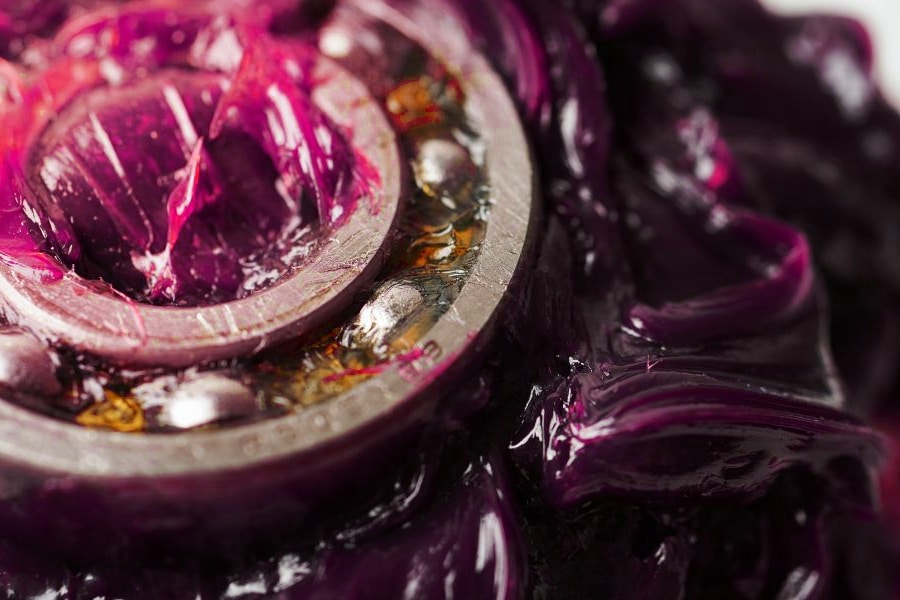
energy efficiency
By providing a lubricating layer between contacting surfaces, the amount of energy required to overcome the resistance to movement of the contacting surfaces is reduced, resulting in more efficient equipment operation and lower energy demand.
Although it is not the main purpose of lubricating a machine, this efficiency comes from the correct use of the lubricant and must be taken into account when calculating the benefits of optimal lubrication.
Sealing
This feature is mainly provided by greases, since their viscosity characteristics protect the lubricated surface from external contaminating particles and seal cracks or other flaws created by wear.
This feature may be especially important if the environment is prone to lubricant leakage, as sealing would prevent this problem as well.
Temperature control
Lubricants flow cyclically at given periods of time, and one of their functions is to act as a heat sink for the heat generated by component movement and friction.
This feature is essential to keep the composition of the metal parts intact and prevent deformation or failure of the system due to excess heat.
Corrosion prevention
Lubricants may possess characteristics that prevent oxygen particles from oxidizing the metals they protect. This not only reduces imperfections, but also protects metals against corrosion, which maintains their integrity, prolongs their lifespan and allows for more efficient and controlled operations.
This is why it is important to apply lubricants resistant to oxidative degradation. Oxidation is a serious problem that can reduce the performance, lifespan, quality and appearance of metals.