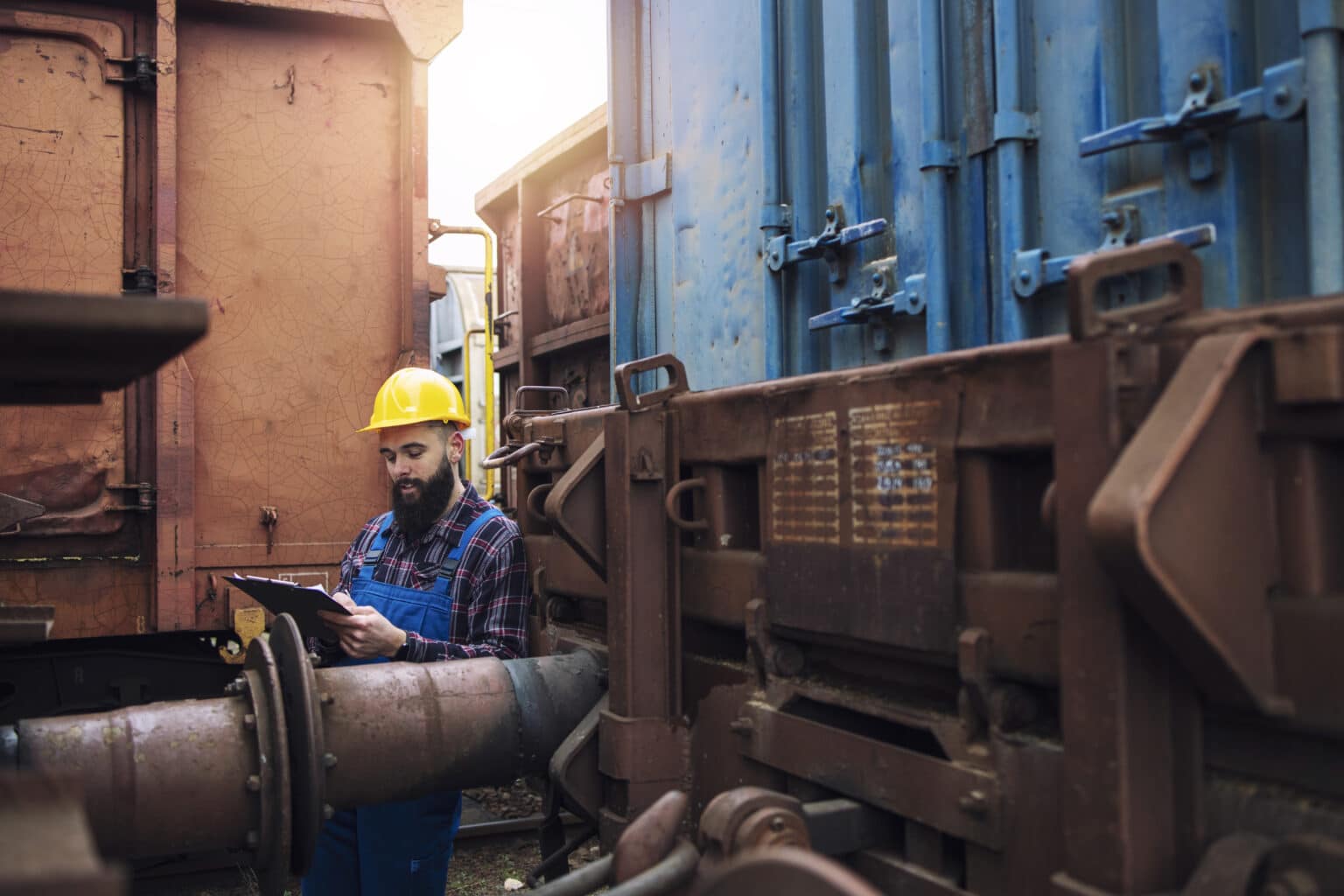
Types of industrial machinery breakdowns and causes
Industrial machinery is at the heart of many manufacturing operations, and its proper functioning is crucial to ensure efficiency and productivity. However, breakdowns in industrial machinery are inevitable and can have a significant impact on production. Understanding the types of breakdowns and their causes is essential to minimize downtime and extend the life of industrial machines. In this article we will explore the most common types of breakdowns and the causes behind these failures, providing detailed insight into how to prevent and manage these problems.
Types of breakdowns in industrial machinery
Each failure in industrial machines can be classified according to the nature of its problems. Depending on the typology of the machine or its operation, we will find different types of failures.
Mechanical failures
Mechanical failures are one of the most common types of breakdowns in industrial machinery. These failures can be caused by natural wear of mechanical components due to continuous use and lack of proper maintenance. Incorrect or insufficient lubrication can trigger overheating and damage moving parts, directly affecting the useful life of the machinery. At Nortek, we give you the necessary service to automate your industrial lubrication processes.
In addition, faulty use and excessive load on machines can lead to breakdowns, causing components to wear out faster than expected. Repairing these mechanical failures often requires specialized technical intervention, which can be costly and time-consuming.
Electrical failures
Electrical failures in industrial machinery can include problems with electrical components such as motors, cables and control systems. These failures can be caused by machine obsolescence, use of faulty components, or improper maintenance. Lack of a preventive maintenance plan can allow minor problems to accumulate, eventually resulting in more serious electrical failures. In addition, errors in software or control system programming can also cause machine downtime. To prevent these breakdowns, it is crucial to perform regular maintenance and ensure that all electrical components are in good condition.
Hydraulic failures
Hydraulic failures are a significant problem in industrial machines that rely on hydraulic systems for their operation. These failures can be caused by lack of lubrication, use of incorrect lubricants or wear on the internal surfaces of hydraulic components. The absence of regular maintenance can allow contaminants to build up in the hydraulic fluid, which can cause severe damage to internal parts. In addition, malfunctioning hydraulic valves or pumps can disrupt industrial processes and lead to serious breakdowns. Implementing a proper maintenance plan and regularly monitoring hydraulic systems can help prevent these failures.
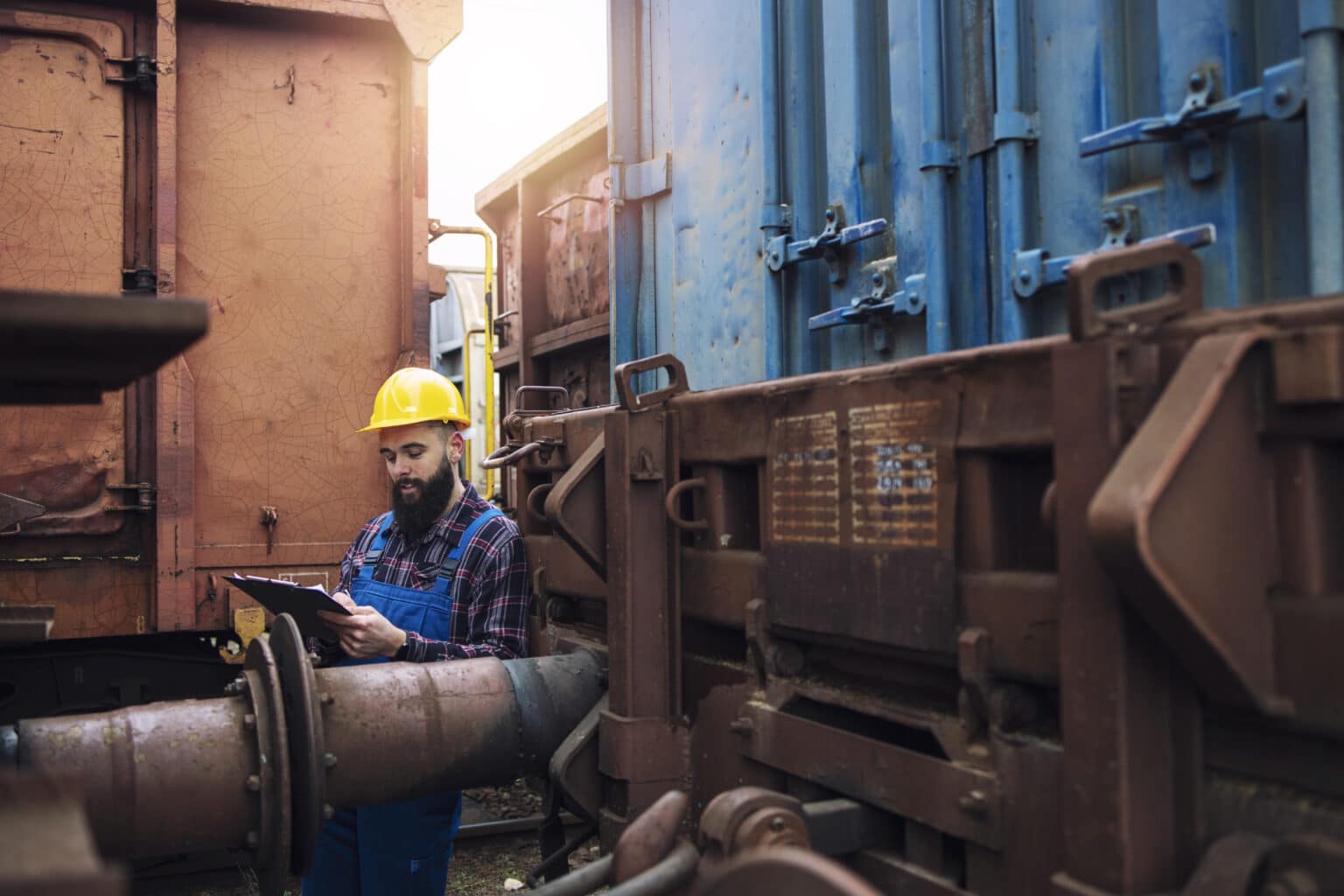
Pneumatic Breakdowns
Pneumatic failures arise in machines that use compressed air to operate. These systems can fail due to clogged air lines, leaks or wear of pneumatic components. Lack of maintenance and moisture accumulation in the system can cause corrosion, damaging internal parts and reducing system efficiency. In addition, continued use without proper supervision can lead to increased wear and equipment failure. To minimize these problems, it is essential to perform regular inspections and keep the pneumatic system clean and well lubricated, thus ensuring optimal performance.
Causes of failures in industrial machinery
Although the nature of failures is often random, we can find certain habits or events that lead to failures on a regular basis.
Lack of maintenance
Lack of maintenance is one of the most common causes of breakdowns in industrial machinery. When preventive maintenance is not performed properly, minor problems can accumulate and trigger more serious machine failures. The absence of a structured maintenance plan can increase the risk of overheating and premature component wear. In addition, neglecting to lubricate and overhaul systems can lead to mechanical and electrical failures.
Component wear
Component wear is a natural consequence of the continuous use of industrial machinery. Over time, moving parts and critical components experience friction and stress, which can lead to their eventual failure. Lack of a properly implemented maintenance program can accelerate this wear, especially if regular lubrication of parts is not performed. Wear can also be exacerbated by improper machine use or overloading. To minimize the impact of wear on machines, it is vital to perform regular shutdowns and replace damaged components before they cause major breakdowns.
Human error
Human error is another significant cause of industrial machine failure. Lack of proper training, inadequate supervision or occasional absent-mindedness can result in the faulty use of machinery, which can cause irreversible damage. Operators may incorrectly program systems or ignore machine warning signals, leading to malfunctions. In addition, pressure to meet production deadlines can lead to shortcuts that compromise machine safety and performance. Implementing continuous training programs and strict supervision can help reduce the incidence of human error and improve machine reliability.
Planned obsolescence
Planned obsolescence is a design strategy in which manufacturers schedule the useful life of their products to become obsolete after a certain period of time. In the context of industrial machinery, this can lead to an increase in breakdowns, as machines are designed to fail after a certain amount of time. This practice can cause an increase in repair and replacement costs for companies, in addition to disrupting industrial processes. To combat planned obsolescence, it is crucial that companies invest in high-quality machinery and establish relationships with manufacturers that prioritize durability and long-term support.
The importance of avoiding machinery breakdowns
Avoiding breakdowns in industrial machinery is crucial to maintaining operational efficiency and reducing costs associated with repairs and downtime. Breakdowns not only affect production, but can also compromise worker safety and delivery schedules. Implementing proper industrial maintenance, along with a preventive maintenance plan, can help identify and fix problems before they become serious failures. In addition, investing in training for operators and upgrading obsolete equipment can minimize the risk of breakdowns. Ultimately, preventing breakdowns in industrial machinery plays a key role in optimizing manufacturing processes and the success of any company.