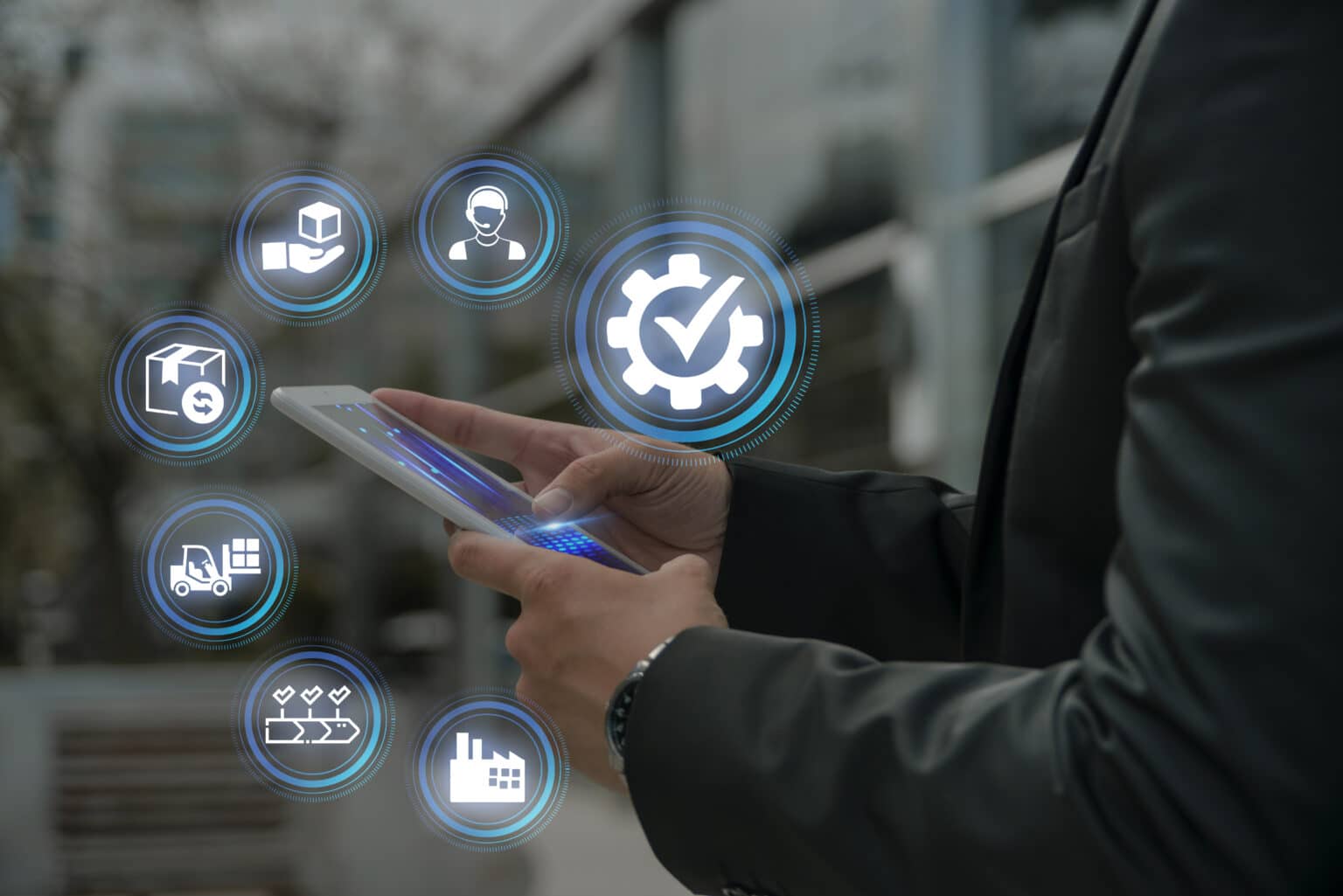
Trends in industrial automation
In today’s changing industrial landscape, industrial automation is emerging as a key pillar to drive operational efficiency and process optimization. As 2024 draws to a close, trends in industrial automation are emerging as key to defining the future of automation, promising not only improved production, but also a sustainable impact and a reduction in the carbon footprint of industries. This article explores how the latest trends and emerging technologies are shaping industrial process automation, providing flexibility, artificial intelligence and real-time data analytics for smarter, more predictive decision making.
What is an industrial automation system?
An industrial automation system consists of a series of technologically advanced processes aimed at optimizing the production and control of industrial processes. These systems integrate tools such as intelligent sensors, robotics and control software to increase operational efficiency and reduce human intervention in repetitive and dangerous tasks. In this context, digitization plays a crucial role, enabling real-time data collection and analysis that drives process optimization. This type of automation and control makes it possible to predict and prevent failures, which is essential for predictive maintenance and the reduction of operating costs, ensuring continuous and smooth production.
Digital transformation has brought industrial automation into a new era where artificial intelligence and the Internet of Things (IoT) act as drivers of change. Thanks to these technologies, automated systems now have the ability to adapt and learn from their environments, making use of machine learning. The implementation of AI not only improves data-driven decision making, but also enables greater flexibility in production and unprecedented customization, responding to the demands of an increasingly demanding and competitive market.
Benefits of automation in the industrial sector
Automation in the industrial sector offers a wide range of benefits including increased operational efficiency, production quality and workplace safety. The implementation of automated systems enables companies to optimize their processes and reduce downtime through predictive and proactive maintenance based on data collected in real time. In addition, automation contributes significantly to sustainability by minimizing waste and reducing energy consumption, both of which are increasingly critical in a work environment that seeks to reduce its carbon footprint.
Another primary benefit is improved competitiveness. Companies that adopt industrial automation can increase their responsiveness to changing market demands through production flexibility. The ability to customize products as consumer trends evolve is a considerable advantage in dynamic markets. Automation also increases safety by reducing workers’ exposure to hazardous environments by delegating those tasks to purpose-built machines and robots, which also reduces the risk of injuries and accidents.
The importance of automating lubrication in industrial processes
Automating lubrication in industrial processes is crucial to ensure optimal and long-lasting operation of machinery. Automated lubrication systems help keep equipment in optimal condition by applying the exact amount of lubricant at the right time, reducing wear and minimizing the risk of mechanical failure. This type of automation not only extends equipment life, but also optimizes operating costs by eliminating the need for frequent manual maintenance, allowing employees to focus on more strategic, high-value activities.
In addition, lubrication automation contributes significantly to sustainability by ensuring that no more lubricant is used than necessary, thus avoiding waste and contributing to more environmentally responsible industrial practices.
Industrial trends in terms of automation
IoT and Industry 4.0 integration.
The integration of IoT and Industry 4.0 is revolutionizing the industrial landscape by offering smarter and more connected automation solutions. IoT technology enables communication between devices and systems, facilitating real-time data collection and providing valuable information for fast and effective decision making. This connectivity is essential for process optimization and the creation of a more efficient and proactive production environment, where prediction and trend analysis are performed continuously and accurately.
IoT, together with Industry 4.0, fosters the adoption of advanced technologies such as artificial intelligence and collaborative robotics, enabling the future of industrial automation. The constant connection and flow of data between devices enables better systems integration, optimizing not only production, but also services such as predictive maintenance. This technological evolution is one of the main trends in industrial automation for 2024, and promises to continue transforming the way industries operate, ensuring a sustainable and adaptable development to future needs.
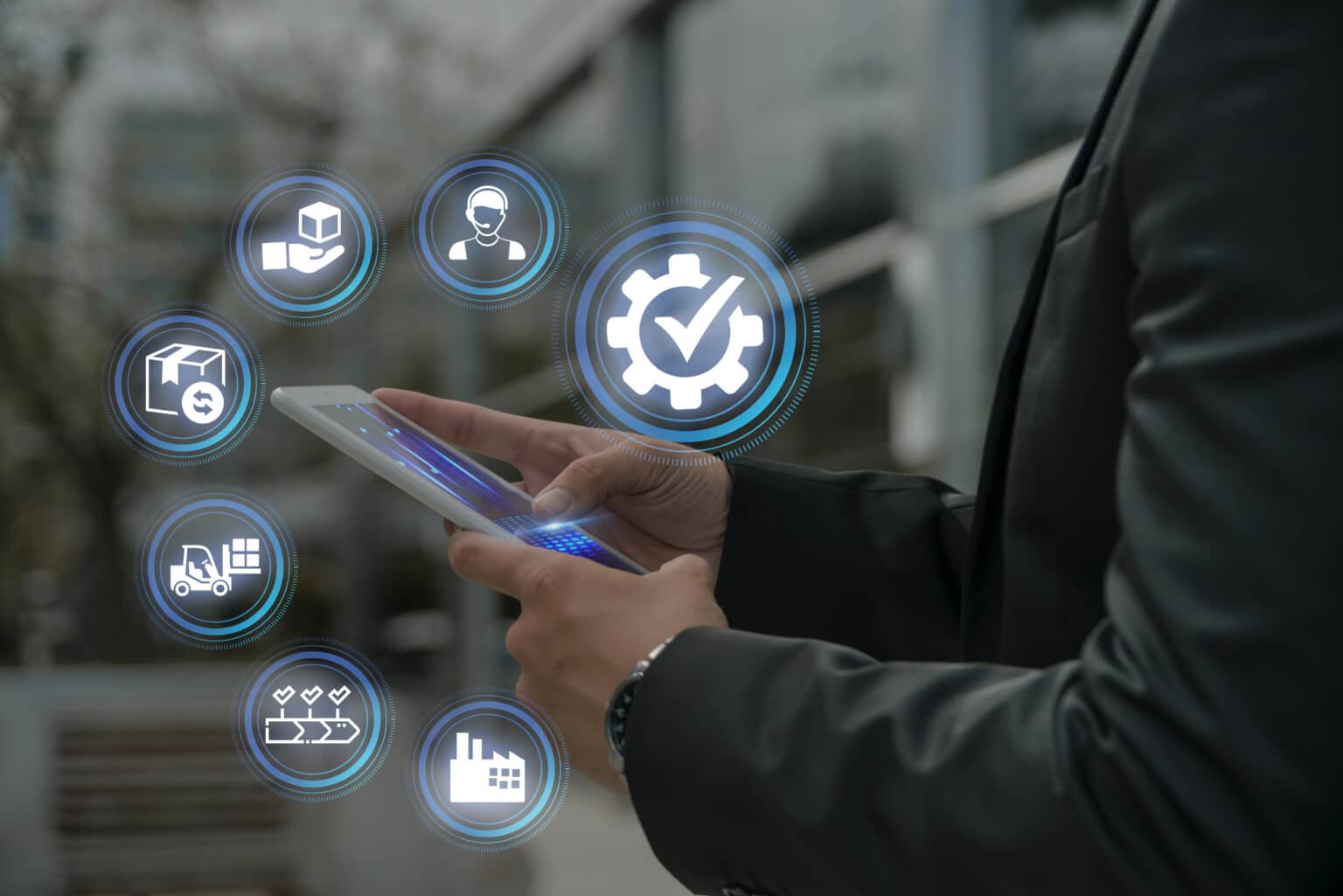
Improvement in collaborative and advanced robotics
Advanced collaborative robotics is transforming production environments by enabling direct human-robot collaboration, increasing productivity and workplace safety. These robots are designed to work in tandem with operators, facilitating tasks that require precision and agility, leading to unprecedented process optimization. In addition, collaborative robotics allows companies to quickly adapt their production lines to new requirements, offering unparalleled flexibility that is key to staying competitive in a volatile market.
Machine learning and real-time data analysis
Machine learning and real-time data analytics are critical components in industrial automation trends, providing an unprecedented ability to understand, predict and optimize production processes. These artificial intelligence systems can analyze large volumes of data to identify patterns and generate accurate predictions, enabling on-the-fly adjustments and improved operational efficiency. The integration of machine learning into industrial automation enables companies to not only respond quickly to market changes, but also to anticipate them, creating a more flexible and resilient production environment.
With real-time data analytics, organizations can monitor ongoing operations continuously, providing immediate information that is crucial for data-driven decision making. This predictive capability translates into more effective process optimization, reducing downtime and improving end-product quality. As these technologies advance, machine learning is expected to continue to be a significant driving force in major automation trends by 2025, enabling a more intelligent and adaptive automation future.
Increased focus on cybersecurity
As industrial automation moves towards greater connectivity, the focus on cybersecurity becomes critical to protect systems against potential threats. With the increase in connected devices and the use of IoT in industry, the attack surface and thus the risk of cyberattacks expands. Therefore, implementing robust cybersecurity measures is critical to safeguard data and ensure uninterrupted operational continuity. Modern systems now integrate these security protocols right from their design, ensuring that every component is protected against potential breaches.
Digital twins for simulation and analysis
Digital twins have emerged as one of the most promising trends in industrial automation, offering a means to simulate and analyze industrial processes in real time. These virtual models replicate physical operations, allowing companies to optimize their procedures before implementing them in the real world. This simulation capability is crucial for prediction and planning, reducing costly errors and improving overall operational efficiency. By incorporating real-time data, digital twins provide a detailed view of every aspect of a product’s lifecycle, from design to production.
Discover our products and services of lubrication for automations
Nortek specializes in providing customized lubrication solutions to meet the demands of industrial processes requiring automatic and semi-automatic lubrication. We understand that proper lubrication is essential for optimum machinery performance, which is why a large portion of our products are designed to operate automatically to ensure maximum operational efficiency.
We offer a complete range of lubrication automation systems, among which centralized greasing systems are the most important. These systems transport grease from an automatic pump through steel pipes to the different points where the machines need lubrication. We also offer air-oil lubrication and oil dehydration solutions, key in the automation of lubrication processes.
If you need more information, please do not hesitate to contact us.