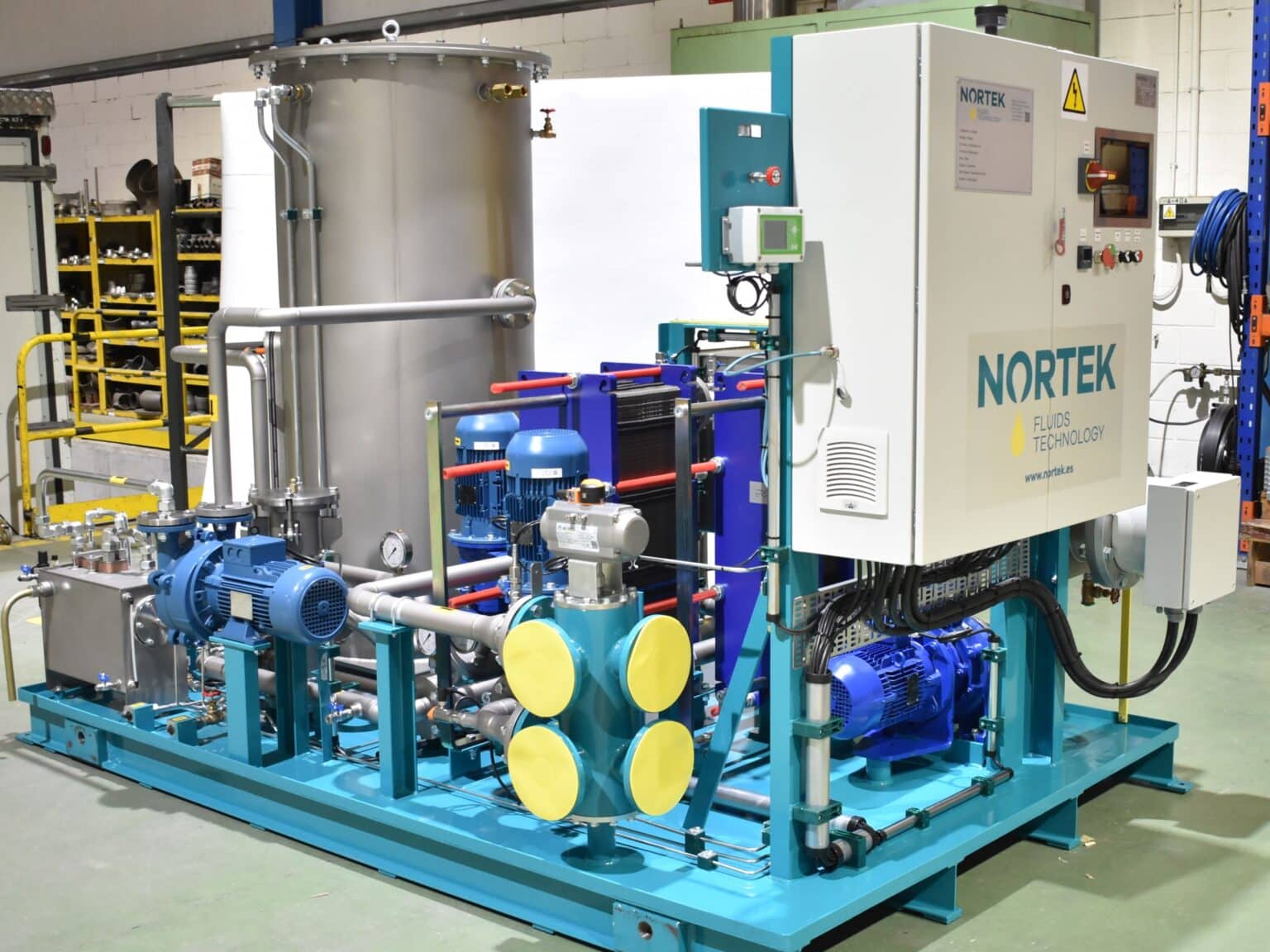
The importance of industrial lubrication
A good lubrication system, accompanied by a planning and study of your industrial machinery, is key to reducing wear of bearings and other parts exposed to friction. This can reduce your maintenance costs by up to 60%.
Keep reading this article to learn more about the role lubrication plays in the proper functioning of your machinery.
What is industrial lubrication?
Industrial lubrication consists of the use of substances, which we call lubricants, that are applied to reduce wear and friction on surfaces that have a regular and constant movement between them.
Although this is the main function of an industrial lubricant, it also performs functions such as corrosion protection, sealing and expelling contaminants from the outside and from the machine wear in mechanical systems, among others.
Although industrial oils and lubricating greases are the most common forms of liquid and semi-solid lubricants, they can also be found in other forms: dry lubricants, gaseous lubricants, etc.
Why is lubrication important?
The importance of lubrication comes from the role it plays in the correct operation of machines. The industrial lubricant acts as an intermediate layer between two surfaces, allowing smooth and efficient movement and greatly reducing the friction generated.
It is not only important to apply it, but also to take into account the way in which it is used, since 80% of the breakdowns in industrial machinery are caused by failures in the way lubrication is supplied. These failures can be caused by a lack or excess of lubricant or by a poor choice of lubricant.
Characteristics of lubricants for industrial machines
Industrial lubricants have many characteristics, each of which gives them properties necessary to increase machine efficiency to its maximum.
These characteristics include the following:
- A low freezing point and a high boiling point: this enables lubricants to maintain their liquid state over a wide temperature range.
- High viscosity index: refers to the resistance of a liquid to the force applied to it. In the case of lubricants, this is a characteristic that must be taken into account, since it is often interesting for the lubricant to remain static on a surface.
- Rapid demulsibility: the ability of any industrial lubricant to separate from water. It is known that oils and other lubricants dissociate easily from water, this property is interesting in order to decontaminate lubricants easily.
- Corrosion and rust prevention: Lubricants also have the ability to protect metal parts from corrosion, rust and oxidation. This is due to its long service life on surfaces and its properties, which depend to a large extent on the additives in the industrial lubricant in question.
How does the lubrication system work?
Each lubrication system has its own way of working. However, all closed lubrication systems have specific components and work in a similar way.
Usually a pump is in charge of sucking and supplying the lubricant to the circuit. The oil is supplied through pipes and distributed to each lubrication point of the installation by a dispenser in periodic lubrication systems or by valves in oil circulation systems.
In addition, the system can include air dosing (air-oil systems), a vacuum dehydration system to decontaminate the oil or a simple drip at the lubrication points of the machinery, among others. This will depend on the needs of each machine.
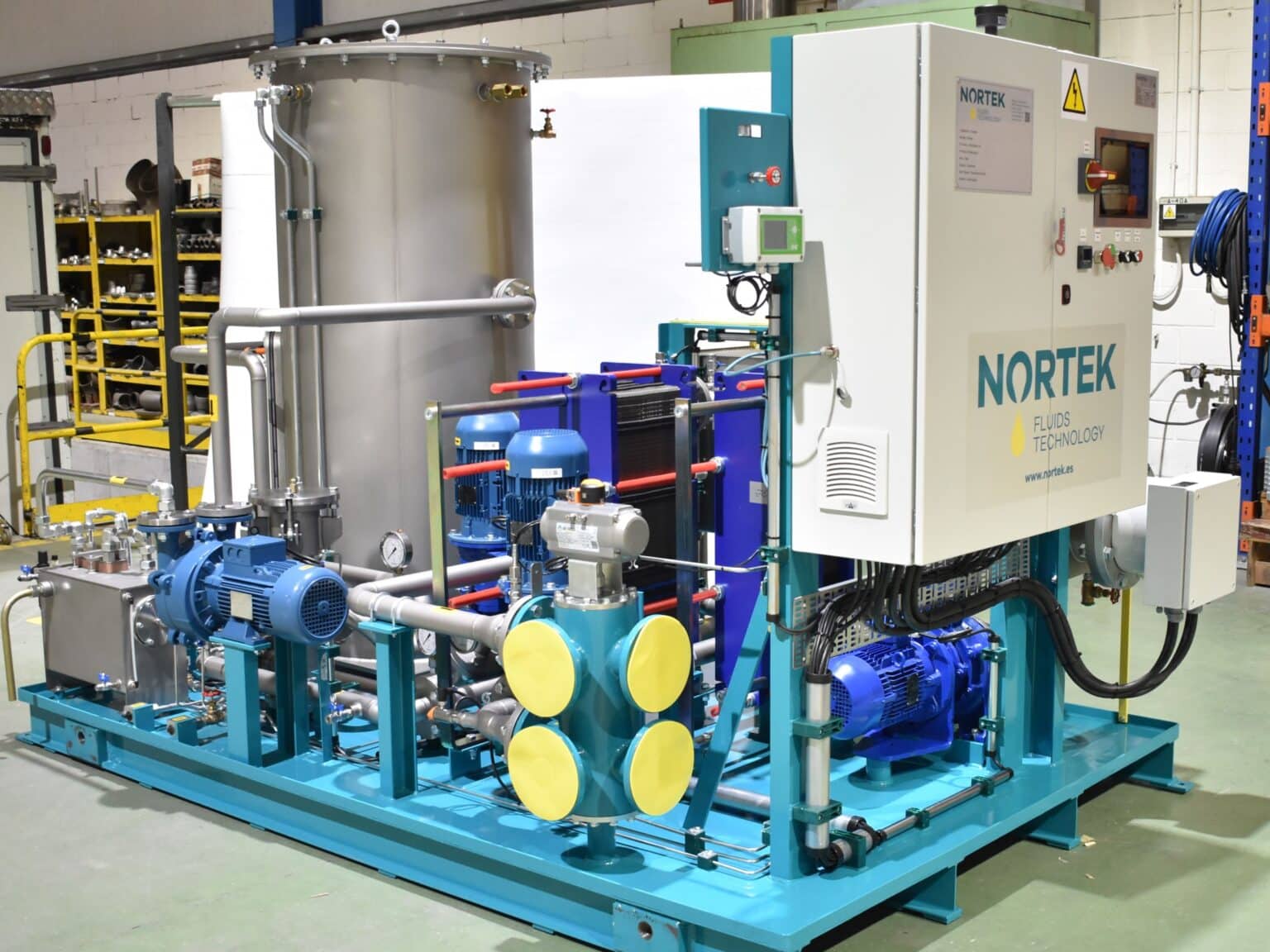
How can lubrication improve the maintenance of industrial machinery?
As mentioned above, a suitable lubrication system adapted to each need can drastically reduce the maintenance investment of each company.
This is because there are no lubricant surpluses or lubrication shortages, which usually result in unexpected shutdowns, production failures and industrial accidents. It also helps to supply the right type of lubricant in a way that best suits each installation, as not all machinery has the same needs in terms of frequency, duration and lubricant characteristics.