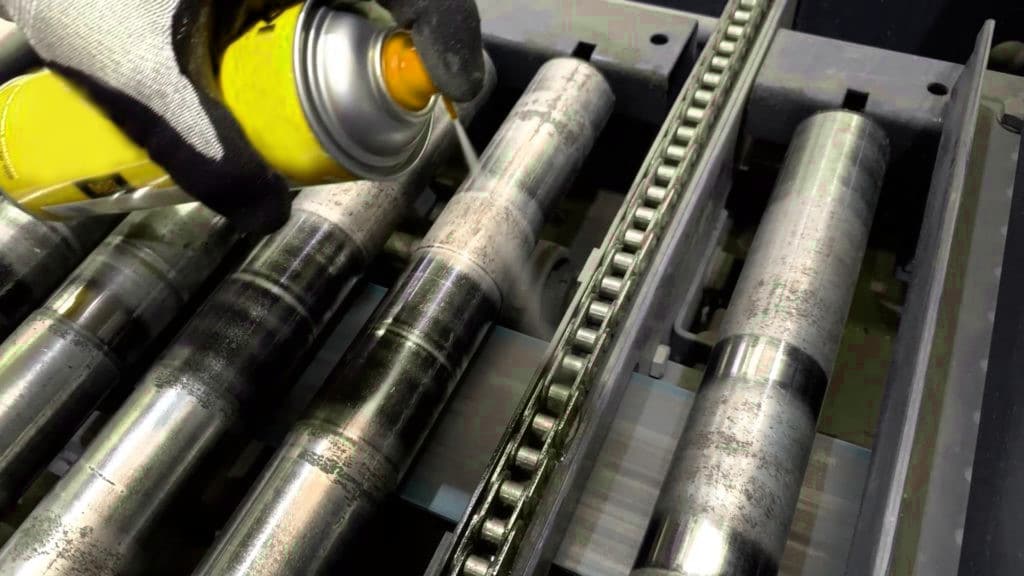
Lubricant raw materials
Lubricants are essential in countless industrial and domestic applications. These products are formulated using a variety of raw materials. The quality of lubricants depends largely on these raw materials, which determine their properties and performance under various conditions. In this article, we will explore the importance of raw materials, the factors that influence the composition of industrial lubricants, the different raw materials used and the benefits of a high-quality lubricant.
The importance of lubricant quality
The quality of a lubricant is directly related to the raw materials selected for its formulation. Using high-quality base oils and specialized additives can significantly improve lubricating properties such as viscosity and oxidation resistance. Manufacturers who invest in high-quality raw materials can offer products that provide better protection against friction and corrosion. In addition, these raw materials can influence the stability of the lubricant at various temperatures, ensuring optimum performance in different industrial applications.
Another crucial aspect is how raw materials affect lubricant formulation for specific applications. For example, lubricating oils designed for gears must contain additives that reduce wear and debris, while hydraulic fluids require properties that maintain cleanliness and minimize sludge formation. Choosing the right raw materials ensures that the lubricant can withstand the demands of the most demanding industrial applications, providing longer service life and more efficient equipment operation.
Factors influencing the composition of industrial lubricants
Several factors influence the composition of industrial lubricants, including operating temperature and desired mechanical properties. Viscosity is a critical property that must be carefully matched to the temperature range in which the lubricant will be used. Base oils and additives play a key role in determining the viscosity index of the final product. In addition, oxidation resistance and corrosion protection are essential factors to be considered during formulation.
The type of machinery or specific application also determines the composition of the lubricant. For example, compressors require lubricants that can operate efficiently under high pressure and elevated temperatures. Conversely, metalworking fluids must be water-soluble to facilitate cleaning and reduce friction on metal surfaces. Specialized additives, such as corrosion inhibitors and wear-preventing compounds, are included to enhance the properties of the lubricant and ensure that it meets the technical requirements of each industrial application.
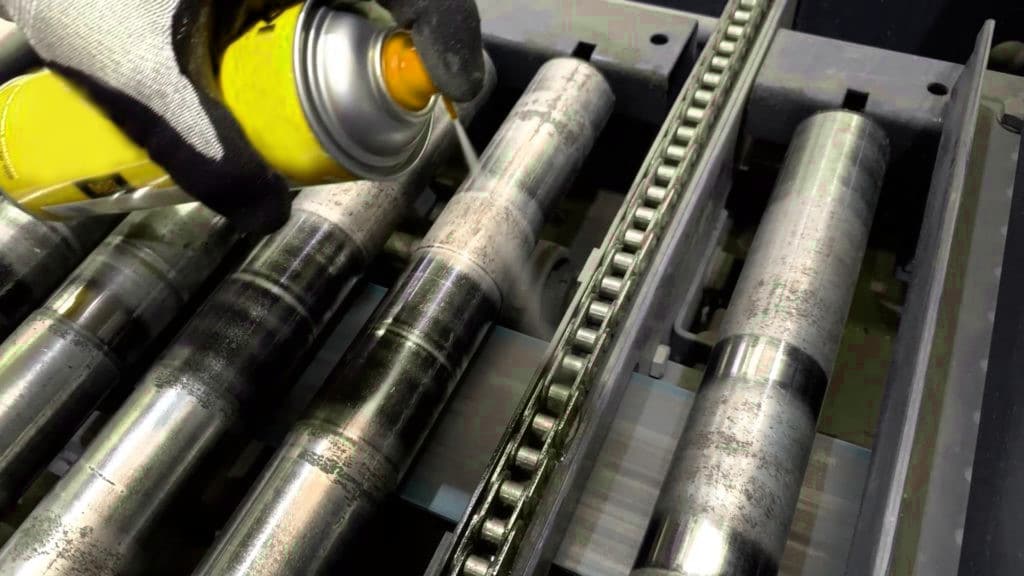
Different raw materials to create lubricants
Raw materials for creating lubricants include a variety of base oils and chemical additives. Mineral oils, derived from crude oil, are a common choice due to their availability and cost. However, synthetic oils, such as PAOs and esters, offer superior advantages in terms of thermal stability and oxidation resistance. These base oils are combined with specialized additives to formulate lubricants that can be adapted to extreme conditions and specific applications. Hydraulic fluids, gear oils and compressor lubricants are examples of products that benefit from these advanced raw materials.
In addition to base oils, additives play a crucial role in improving the properties of lubricants. Anti-wear additives and corrosion inhibitors are essential for protecting metal surfaces and extending equipment life. Other additives, such as viscosity modifiers and cleaning agents, ensure that the lubricant maintains its performance over a wide range of temperatures and operating conditions. Selecting the right raw materials enables manufacturers to design lubricants that meet the most demanding standards and provide reliable, long-lasting performance.
Benefits of a quality lubricant
A high-quality lubricant offers numerous benefits, including increased protection against wear and friction. This translates into longer equipment life and reduced maintenance costs. Quality lubricants also contain additives that improve resistance to rust and corrosion, which is crucial for industrial applications where equipment is exposed to harsh conditions. In addition, these lubricants provide improved thermal stability, allowing them to be used over a wide temperature range without degrading or losing effectiveness.
Another significant benefit is the energy efficiency provided by high-quality lubricants. By reducing friction between metal surfaces, these lubricants can improve equipment performance and reduce fuel consumption. This is not only beneficial from an economic point of view, but also contributes to sustainability and the reduction of pollutant emissions. Finally, high-quality lubricants are generally cleaner and less prone to sludge and residue formation, which helps to keep systems and components in optimal operating condition.