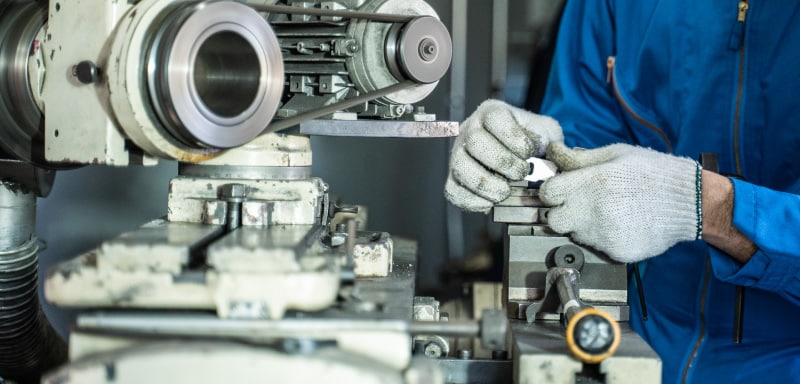
All about industrial machinery maintenance
Industrial maintenance is a fundamental pillar for any company in the sector. It not only ensures maximized efficiency, but also increases safety in installations and longevity of equipment and machines. Proper maintenance of industrial assets can make the difference between the success and failure of any operation.
In this article, we will analyze in detail each of the dimensions and variants of industrial maintenance, its benefits and how to implement it effectively and efficiently. Read on to find out everything you need to know about it.
What is industrial maintenance?
We define industrial maintenance as the set of actions necessary to ensure that industrial facilities, machines or work equipment that need it, work properly. Typical actions include inspection, lubrication, cleaning or repair of components in order to avoid short and long term problems.
Maintenance must be applied both passively and actively, in order to anticipate and correct all possible failures that may arise at any given time. This is why different types of industrial maintenance are distinguished.
Types of industrial maintenance
There are different types of industrial maintenance. Each of them has a specific maintenance task and plays a crucial role in ensuring that your machinery has the longest possible service life and the fewest possible downtime.
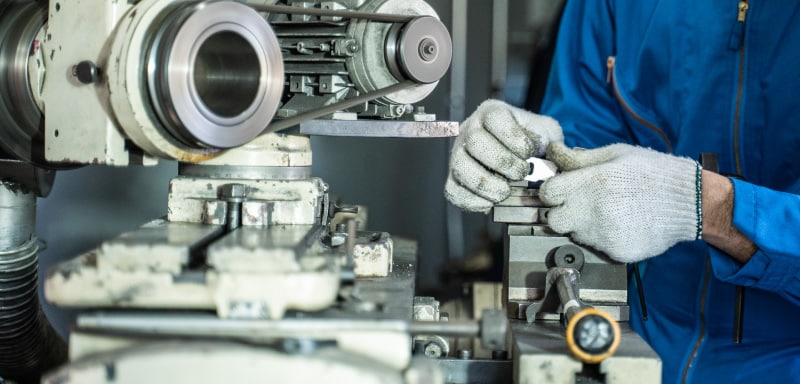
Preventive maintenance
Preventive maintenance consists of a set of actions carried out repeatedly to verify that the operation of the machines is running correctly, without any type of breakdown that could cause more serious failures in the future.
Components related to calibration, electricity, mechanics and many others are usually checked. This depends on the function of the company and the characteristics of each machine.
This type of maintenance is the most common and the most frequently repeated. This is because it is not caused by a malfunction of the machine, but by its own systemic nature.
Corrective maintenance
Corrective maintenance basically consists of the operations and actions carried out in a facility in order to repair or fix machines that have suffered breakdowns.
This type of maintenance does arise as a result of a failure that could not be corrected preventively or that has arisen sporadically. It is more standardized than it may seem, since it is a type of maintenance that we apply in many other areas.
Predictive maintenance
Predictive maintenance is a somewhat more advanced strategy than the other two, as it uses more complex monitoring and data analysis techniques to predict potential failures before they occur.
It differs from preventive maintenance in the frequency of measurements. Preventive maintenance is performed periodically; however, predictive maintenance takes real-time data through the use of sensors, analysis software and other maintenance equipment.
Total Productive Maintenance (TPM)
Total Productive Maintenance or TPM is a redefinition of the concept of industrial mechanical maintenance for any type of plant or facility that needs it. The objective of this applied maintenance program is to significantly increase both production and employee motivation at work. This is done through an emphasis on preventive maintenance.
This program creates a shared responsibility for each of the teams, which encourages worker participation in the facility. This can be very effective in order to incentivice a productivity improve.
Benefits of industrial maintenance
One of the main benefits of industrial maintenance is the improvement in long-term opex and capex. This is because the investment required for efficient maintenance performance is far lower than the investment required to fix machines, replace them or cover downtime losses.
In addition, in many sectors within the industrial world, a failure can cause serious problems for the safety of the environment and workers. A maintenance system can prevent these failures, as well as minimize their impact should they occur, thus increasing the safety of the working environment.
How to implement a maintenance plan?
A maintenance plan consists of a complete set of instructions designed to keep equipment, machinery and any other industrial asset in optimal operating condition.
We can define 6 steps for its elaboration:
- Set objectives: they must be measurable and achievable.
- Define KPIs: in this area you could use meters such as MTBF (mean time between failures) or downtime.
- Have an inventory of assets: they must be hierarchical and classified.
- Establish a budget: it must take into account the company’s resources and estimated costs.
- Use software for analysis: Computer-assisted maintenance management software (CMMS) can significantly improve the planning and tracking of maintenance activities.
- Perform periodic reviews and adjustments: this will make the maintenance system more and more accurate and adapted to our real problems.
All of this will be subject to the budget and size of the company, but maintaining an adequate maintenance investment will more than repay the investment in the medium and long term.