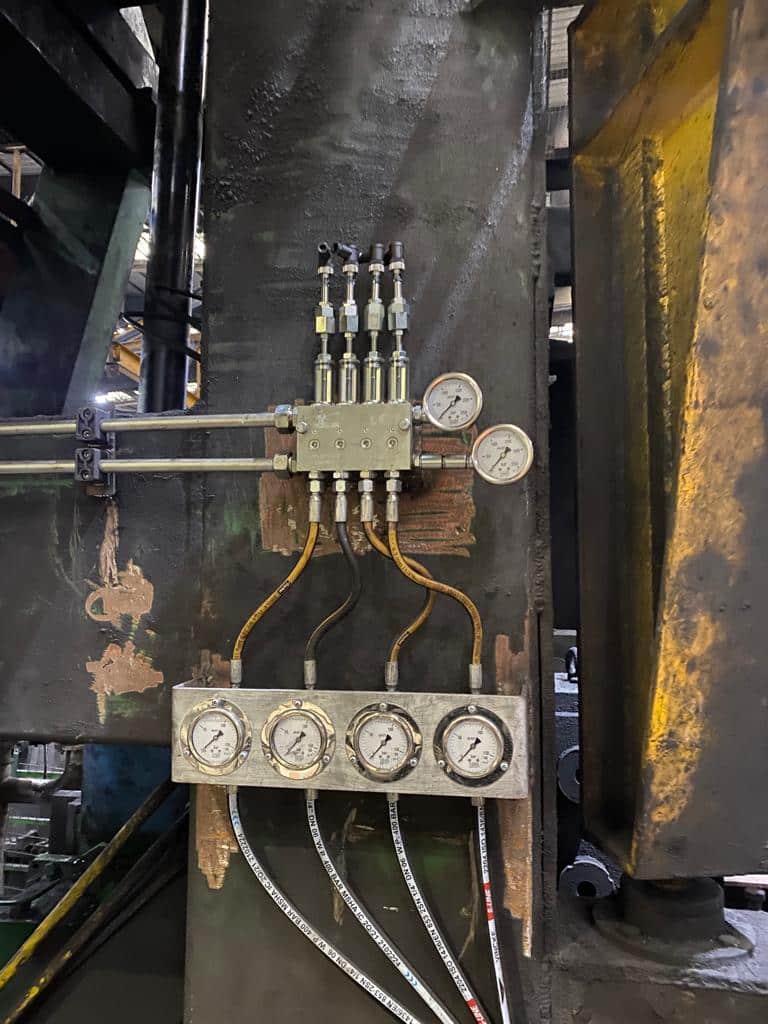
Best lubrication solutions for the Iron and Steel industry
The iron and steel industry is a fundamental pillar of world economic development, producing essential materials for various sectors. In this context, proper lubrication becomes a critical factor to ensure the efficiency and longevity of machinery and equipment used in manufacturing processes. This article explores the best lubrication solutions to meet the specific challenges of this industry, ensuring high performance and extending equipment life under extreme conditions.
Why is lubrication critical in the iron and steel industry?
Lubrication in the iron and steel industry is essential due to the extreme conditions in which its equipment operates. Steel and metal manufacturing processes require effective friction reduction to avoid premature wear of components. Industrial lubricating oils and fluids act as a protective barrier that not only reduces friction but also protects against corrosion. This is vital to optimize operational efficiency and maintain the high performance of equipment under extreme pressure conditions.
In addition, proper lubrication helps extend the life of components such as gears and bearings, which is crucial for minimizing downtime. A good industrial lubrication system also ensures that greasing is consistent and effective, which is critical for continuous operation. In an environment where downtime can translate into significant losses, the importance of good lubrication cannot be underestimated.
Main lubrication challenges in iron and steel processes
One of the main lubrication challenges in the metalworking industry is handling the high temperatures and extreme loads experienced during metalworking machining. Conventional lubricants can degrade rapidly under these conditions, so high-quality lubrication solutions are required. Specialty additives and synthetic lubricants are critical to maintain lubrication stability and effectiveness under these adverse conditions.
In addition, contaminated environments represent another significant challenge. Dust, moisture and metal particles present in the working environment can compromise the efficiency of lubrication systems. This requires the use of oils and fluids that can resist contamination and continue to function efficiently. Choosing industrial lubricants that can meet these challenges is crucial to ensure operational reliability and prolong equipment life.
High temperatures and extreme loads
High temperatures and extreme loads are common conditions in the iron and steel industry, especially in processes involving furnaces and forges. Under these circumstances, friction between metal parts can increase considerably, which could lead to accelerated wear without proper lubrication. High-quality lubricants, especially those formulated for extreme pressure conditions, help reduce friction and protect critical components.
The use of synthetic lubricants with special additives is an effective strategy to improve heat resistance and stability under load. These additives not only reduce friction, but also act as coolants, helping to dissipate heat generated during operation. This optimizes equipment performance, minimizes the risk of failure and extends component life, ensuring safer and more efficient operation.
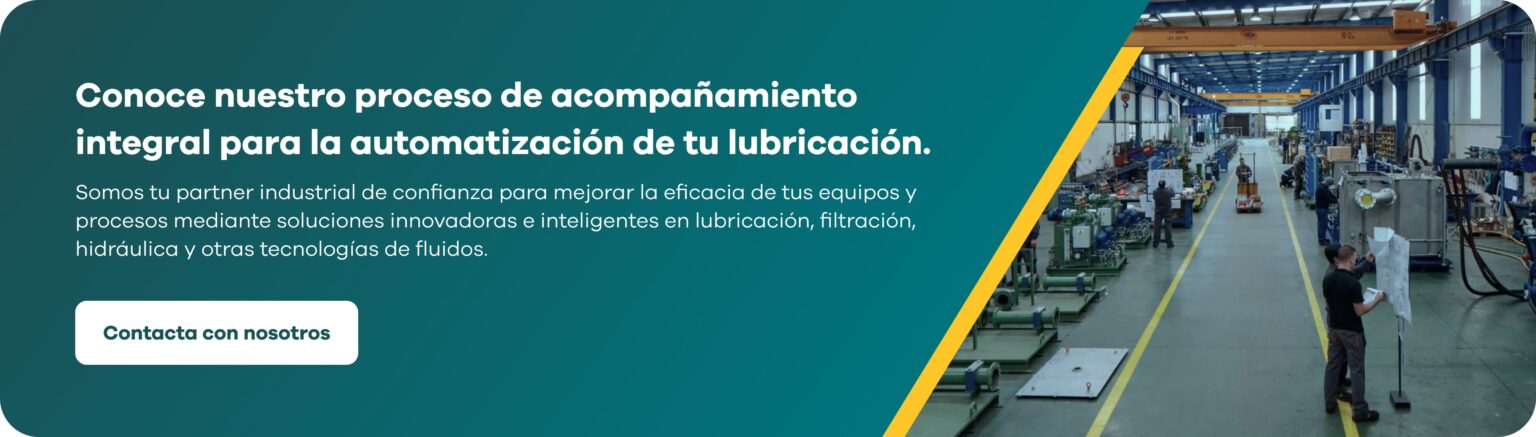
Contaminated environments: dust, humidity and metallic particles
The presence of dust, moisture and metal particles in the environment can severely affect the effectiveness of lubrication systems. These contaminants can infiltrate oils and fluids, degrading their ability to reduce friction and protect against corrosion. In such circumstances, it is vital to use industrial lubricants specifically designed to resist contamination and maintain their effectiveness.
Lubrication systems must be equipped with high quality filters and seals to prevent the entry of contaminants. In addition, the choice of a suitable lubricant, capable of maintaining its integrity in the presence of metal particles and moisture, is crucial. This not only ensures the continuous and reliable operation of equipment, but also helps to extend the service life of critical components and reduce unplanned downtime.
Continuous operation and reliability requirements
Continuous operation is a crucial aspect in the iron and steel industry, where operations are often carried out 24 hours a day. Equipment reliability is essential to avoid interruptions in production. This is where industrial lubrication systems play a vital role. A well-designed lubrication system ensures that all moving parts are adequately lubricated, which minimizes friction and wear.
The implementation of advanced automatic lubrication solutions ensures that lubrication is accurate and consistent, even during prolonged operations. This not only optimizes equipment performance, but also reduces the need for downtime, making it critical to your predictive maintenance plan. By ensuring that components are always well lubricated, operational efficiency is improved and the risk of failure is minimized, ensuring uninterrupted production.
Most effective types of lubricants for the steel and metal industry
In the iron and steel industry, the choice of the right lubricants for each metal is essential to ensure efficient operation of equipment. Synthetic lubricants, known for their ability to withstand high temperatures and extreme pressures, are highly recommended. These lubricants are formulated with special additives that reduce friction and prevent corrosion, which is essential to optimize the service life of metal components.
- High temperature lubricants: Ideal for furnaces, hot rolling mills and other applications where extreme temperatures can degrade common lubricants.
- Synthetic-based greases: Provide excellent thermal stability and resistance to oxidation, especially useful in bearings and mechanisms exposed to heavy loads.
- High viscosity mineral oils: Used in centralized lubrication systems, they offer good protection in dusty and high load environments.
- Solid lubricants: Efficient in extreme conditions where liquid lubricants fail, such as in forging or pressing processes.
- Biodegradable lubricants: Increasingly adopted for their low environmental impact, without sacrificing performance in many industrial applications.
Advanced lubrication solutions for the steel industry
At Nortek, we are specialists in lubrication solutions for industrial environments related to the iron and steel industry. These are some of the solutions we offer:
Centralized lubrication systems
Centralized lubrication systems are an advanced solution that offers multiple benefits for the steel industry. These systems are designed to provide consistent and accurate lubrication to all critical machinery components. Centralizing the lubrication process ensures that each part receives the right amount of lubricant at the right time, optimizing performance and extending equipment life.
In addition, the automation of these systems eliminates the need for manual lubrication, reducing the risk of human error and improving safety in the working environment. These systems are equipped with advanced sensors and controls that monitor lubricant status and adjust flow as needed, ensuring continuous and efficient operation. Implementing a centralized greasing system not only improves equipment reliability, but also reduces maintenance costs and downtime.
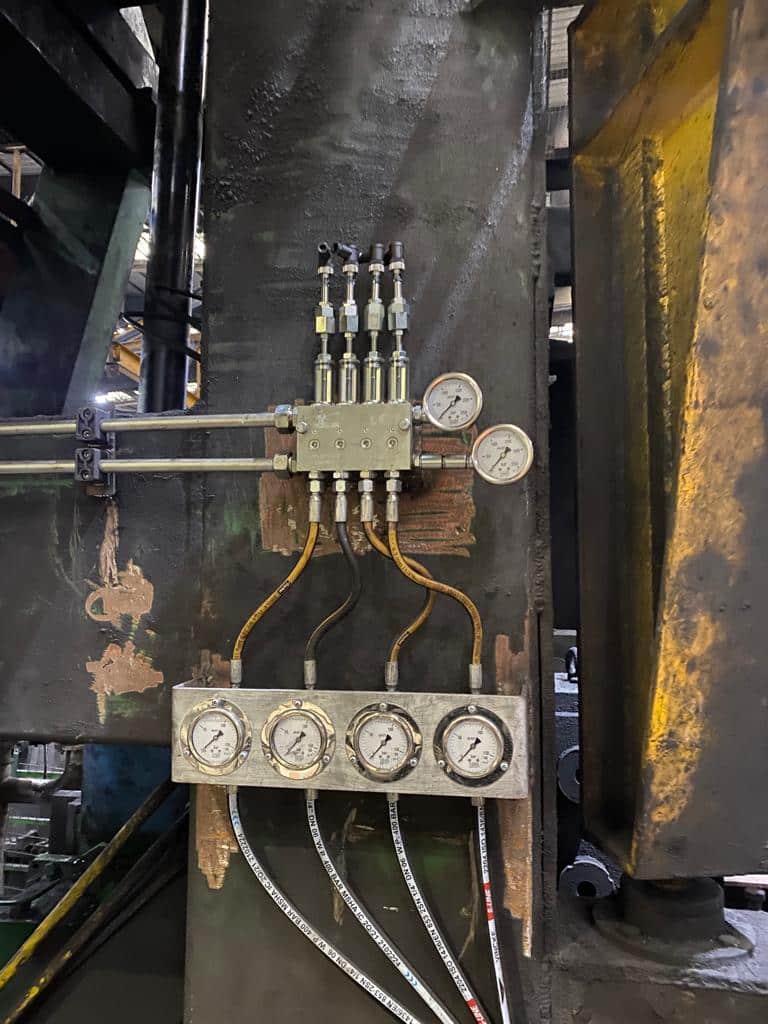
Air-oil systems
Air-oil systems are an innovative option for lubrication in the steel industry, especially in applications where precise lubricant control is critical. This system uses a mixture of air and oil to provide efficient lubrication, reducing friction and wear on components. The ability to adjust the air/oil ratio allows for customization to suit the specific needs of each application.
These systems are particularly useful in high temperature and pressure conditions, where other lubrication methods might fail. By reducing the amount of oil used, the risk of contamination is minimized and operational efficiency is improved. In addition, air-oil systems contribute to greater energy efficiency, as the lubricant flow is optimized to reduce energy consumption. This not only improves equipment performance, but also contributes to environmental sustainability by reducing resource use.
Oil circulation systems
Oil circulation systems are essential to maintain operational efficiency in the steel industry, especially in equipment subjected to high temperatures and heavy loads. These systems ensure a continuous flow of oil, which helps dissipate heat and maintain an even temperature in the components, preventing overheating and possible mechanical failure. Constant oil circulation also ensures that additives are evenly distributed, providing comprehensive protection against wear and corrosion.
In addition, these systems are designed to filter contaminants, maintaining oil quality and extending oil life. The ability to control and monitor oil quality in real time allows for quick intervention in case of need, minimizing the risk of unexpected shutdowns. Oil circulation systems are a valuable investment for any steelmaking operation, improving equipment reliability and efficiency while reducing maintenance costs and extending lubricant life.
Oil emulsion systems
Oil emulsion systems are a combined cooling and lubrication solution, ideal for applications that generate a large amount of heat. These systems mix oil with water to create an emulsion that provides excellent cooling and lubrication capabilities. The emulsion helps reduce friction and wear, keeping components at an optimum temperature and preventing overheating during intensive machining processes.
These systems are especially beneficial in applications where high speed and accuracy are critical. The ability to adjust the ratio of water to oil allows for customization to specific process needs, ensuring that components receive the proper level of lubrication and cooling. By improving operational efficiency and extending equipment life, oil emulsion systems have become a preferred solution in the steel industry.
Vacuum dehydration systems
Vacuum dehydration systems are essential to maintain lubricant quality in environments where moisture is a problem. These systems remove water from the lubricating oil, preventing corrosion and deterioration of metal components. Moisture removal not only improves lubricant efficiency, but also extends equipment life, reducing the need for costly repairs.
These systems work by creating a vacuum that draws water out of the lubricant, ensuring that the oil remains in optimum operating condition. The ability to remove contaminants and maintain oil quality is crucial to equipment reliability in the steel industry. By implementing vacuum dehydration systems, companies can ensure optimal equipment performance, minimize downtime and maximize the life of their lubrication investments.
Tangible benefits of proper lubrication
Proper lubrication offers multiple tangible benefits to the steel and metal industry. By reducing friction and component wear, equipment life is extended, resulting in lower replacement and repair costs. In addition, by optimizing equipment performance, operational efficiency is improved, which can increase productivity and profitability of operations.
Corrosion protection provided by high-quality lubricants is also crucial to maintaining the structural integrity of machines under extreme conditions. By minimizing the risk of failure, downtime is reduced, which is essential for maintaining a steady production flow. Together, these benefits contribute to significantly improving the sustainability and competitiveness of the metalworking industry, ensuring that it can meet the growing demand for steel and metal products with maximum efficiency.